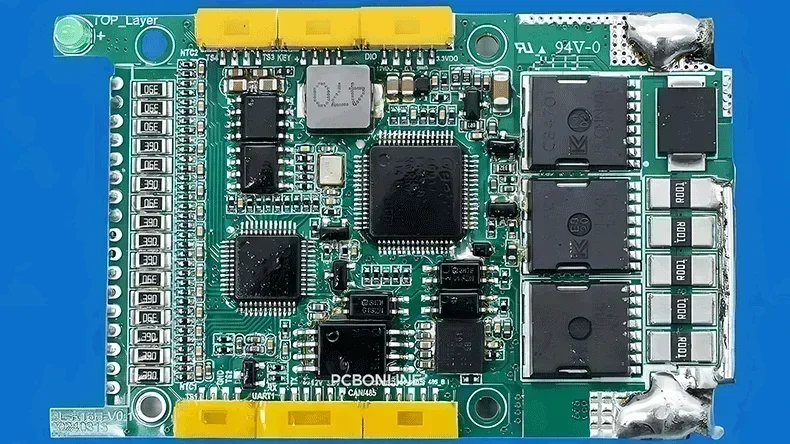
For electric vehicles, including electric cars, motorcycles, trucks, and boats, and modern solar energy systems, the safe and efficient operation of the batteries relies on a system/module -- battery management (BMS). The battery management system monitors the batteries' temperatures and voltages and manages the pack's status.
In the blog, the advanced PCB assembly (printed circuit board assembly) and BMS manufacturer PCBONLINE will explain what a BMS for electric vehicles is.
What is BMS for Lithium-Battery Pack
In the lithium-ion battery pack, there are the main electronic modules: the batteries (cells) connected in groups in parallel and series, the cell contact system, and the BMS (battery management system).
The BMS is the brain of the battery pack. It monitors and manages the operating status of the batteries to ensure that the battery pack operates safely, stably, and efficiently.
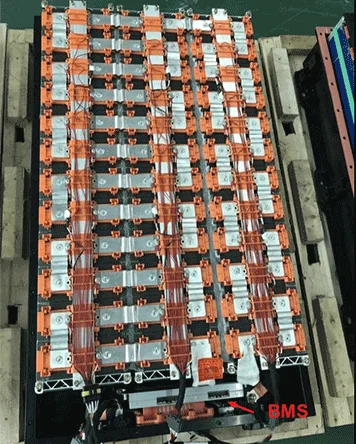
In an electric vehicle, the battery management system receives circuit current signal changes returned from the CCS, reflecting the temperature changes in the batteries/cells. It then analyses and controls the work status of the battery pack to prevent the batteries from overheating and overcooling.
Besides, the BMS measures the voltages in different cells. During slow charging, the currents flow through the CCS traces to the cells, and the power stored in the cells should be within an even range. But when some batteries reach 100% power, some still are 98% or 99%. The BMS measures the voltages, stops charging the 100% cells, and keeps charging the rest until they reach 100%. In this way, the battery management system prevents overcharging. During discharging to power the motor drives, the BMS also monitors the voltages in the cells to prevent over-discharge.
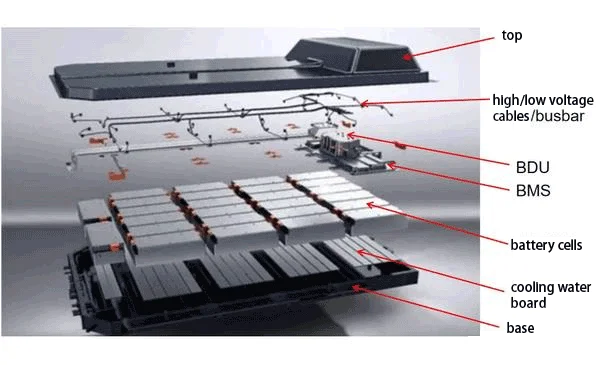
A BMS is a PCBA (printed circuit board assembly) in the battery pack. The main components mounted on the BMS printed circuit board include:
- Microcontroller (MCU): It gathers and processes current signals from the CCS to monitor the voltages and temperatures of the cells. Besides, it controls safety protocols to protect the battery pack from overcharging, overheating, and over-discharging.
- Differential Op-amps: They measure the voltage differences between the cells. During battery pack assembly, the manufacturer will test with them to ensure the cells operate within a different standard range. When charging the EVs, these op-amps also measure the voltage differences and transfer signals to the MCU.
- Rail-to-rail high-voltage Op-amps: They read and output the voltage signals from almost zero to the highest voltage in the BMS. Even though the battery management system for EVs runs at 400V and above and hybrid EVs at 200V and above, the rail-to-rail high-voltage op-amps can amplify the small voltage signals from the current sensors.
Besides the above main components, a BMS, which is a high-voltage PCBA, has components like resistors, capacitors, inductors, connectors, busbars, and heat sinks, depending on the design.
Functions of a Battery Management System
A battery management system plays a critical role in the battery pack for EVs and hybrid EVs. The functions of a battery management system include:
1. Ensure safety: The battery management system prevents the cells from overcharging, over-discharging, overheating and short circuit. Thereby, it protects the battery pack from damage and avoids potential risks.
2. Real-time monitoring: The BMS monitors the cell voltages, currents, and temperatures in real-time to ensure that the cells run in safe operating conditions.
3. Data management: The BMS generates and reports the cell data, such as the battery status, health status, and charge status. It provides information for battery performance evaluation and fault diagnosis.
4. Battery balancing: The battery management system ensures that the power of the batteries remains consistent to prevent performance degradation or safety problems.
5. Charge and discharge management: The BMS controls the battery charging and discharging process, optimizes the battery performance, and extends the battery life.
6. Communication interface: Besides protection and management, the BMS exchanges data with other parts of the EV or solar energy system. Through the communication interface, it achieves seamless integration with the vehicle or system.
7. Intelligent algorithm application: An advanced BMS applies algorithms to optimize charging and discharging strategies, predict battery life and performance, and improve the efficiency and safety of the battery pack.
8. Remote monitoring and cloud technology: Through remote monitoring and cloud computing technology, BMS realizes real-time tracking and data analysis of battery status, and supports remote diagnosis and maintenance.
9. Integration of AI big models: Combined with artificial intelligence (AI) big models, the BMS further improves its prediction capabilities and decision support in complex environments through deep learning and data mining.
The battery management systems are used in EVs, energy storage systems, industrial and marine applications, telecommunications and data center backup power systems, large-capacity mobile power supplies, power tools, two-wheeled travel tools, robots, etc. Through these functions, the BMS not only improves the performance and life of the battery but also ensures safety during use.
One-Stop Battery Management System Manufacturer PCBONLINE
If you want battery management systems to develop your battery packs for EVs, hybrid EVs, solar energy systems, etc, you can work with PCBONLINE for one-stop BMS R&D and manufacturing.
PCBONLINE is a source factory manufacturer, with two large advanced PCB manufacturing bases, one PCB assembly factory, reliable supply chains, and an R&D team for BMS development.
PCBONLINE can provide all the R&D for your BMS project according to your battery pack specification and feature requirements or take part in your development from the early stage.
PCBONLINE manufactures the BMS PCB, sources components, and provides turnkey PCB assembly until the battery management system is made and tested with success.
Besides PCBA manufacturing, PCBONLINE has long-term cooperation with the top 3 mold and enclosure manufacturers to provide custom molds and enclosures for BMS manufacturing.
What's more, PCBONLINE has rich experience in CCS manufacturing and can develop both the CCS and BMS together for your battery pack.
PCBONLINE offers free prototyping/sampling and PCBA functional testing for BMS massive production and can solve all issues to ensure smooth processes and successful results.
To get a quote for your BMS project, please contact info@pcbonline.com. And, see the battery management systems we've successfully manufactured below!
Battery Management System Examples
PCBONLINE has so far developed and manufactured quite a few battery management systems. Below, you can see some BMS pictures that have been allowed by our customers to show.
Below, there are 5 examples of battery management systems we made.
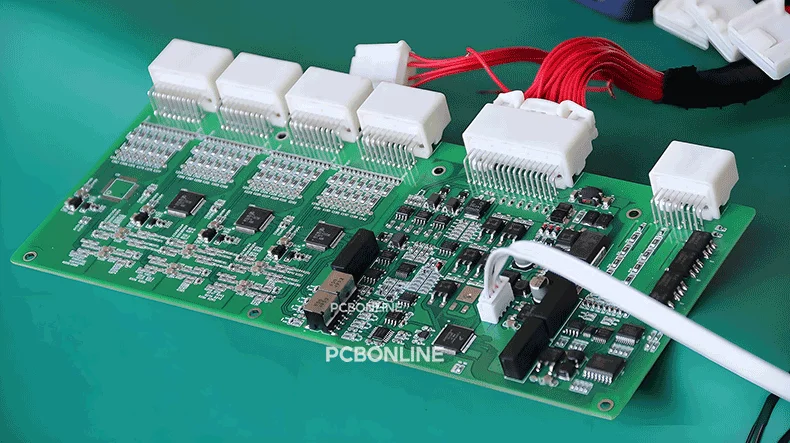
battery management system example 1
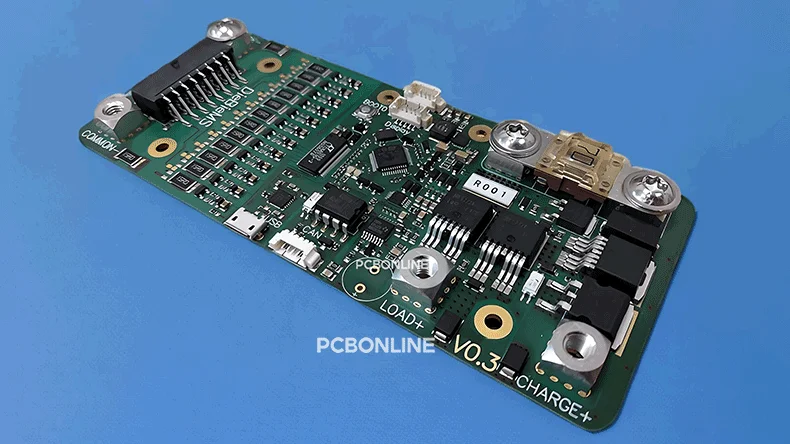
battery management system example 2
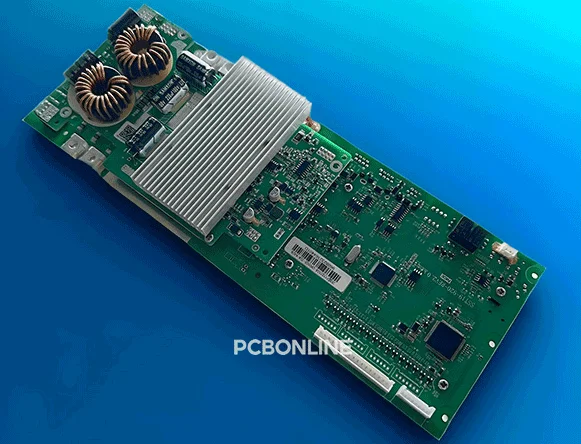
battery management system example 3
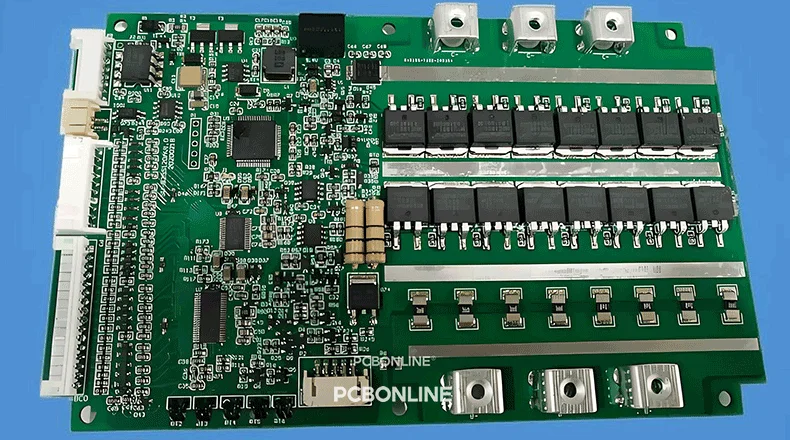
battery management system example 4
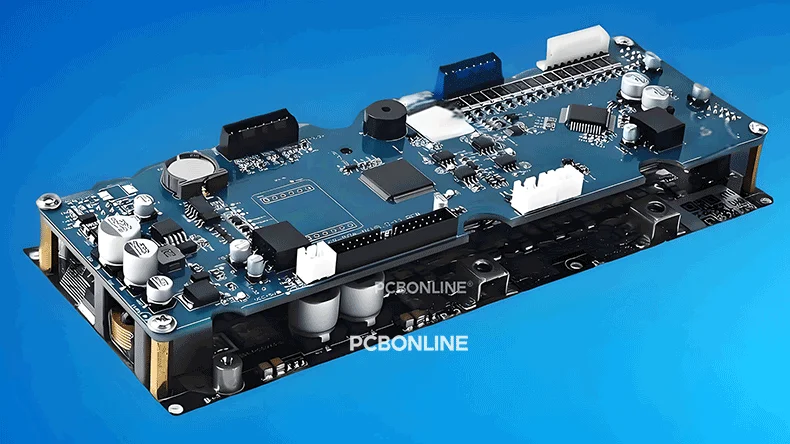
battery management system example 5
Having viewed the battery management system examples, don't hesitate to chat with PCBONLINE about your BMS plan!
Conclusion
A battery management system is a high-voltage PCBA with various components mounted on it. It acts as the brain of the lithium-ion battery pack for EVs, solar energy systems, etc. If you want battery management systems for your custom battery packs, contact the one-stop BMS manufacturer PCBONLINE by email or from the online chat window.
Battery Management System Manufacturing at PCBONLINE.pdf