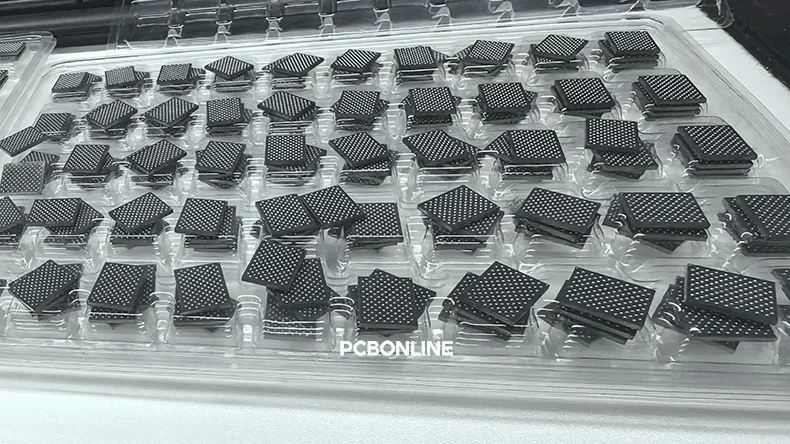
A few months ago, a client sent us a batch of second-hand BGAs and required us to replace solder balls and use them for his PCB assembly project. As electronic components take up the most in the PCB assembly cost, and ICs are the most expensive in the components, these BGAs SAVES BIG for the product fabrication.
The process of placing new solder balls at the bottom of the BGA to refurbish it is called BGA reballing. In this article, the one-stop PCBA manufacturer, PCBONLINE, reveals all about BGA reballing and re-new BGAs for PCB assembly and box-build assembly.
In this article:
Part 1. What BGAs Can Be Reballed? Part 2. BGA Reballing Process Part 3. BGA Reprogramming after BGA Reballing Part 4. WBGA Reballing Service and PCB Assembly Under One RoofWhat BGAs Can Be Reballed?
First of all, let's understand what BGAs can work after the BGA reballing process.
BGA reballing only replaces the solder balls at the bottom of the package for soldering the BGA on the PCB. It does not repair the functional problems of the chip itself.
If the BGA chip itself is still good but its original solder balls are loose or damaged, BGA reballing can restore the BGA solderability.
However, if the chip has been broken, for example, it has any open-circuit or memory unit failure, the BGA can't be fixed by BGA reballing.
In the below scenarios, you can bring life to the used BGAs:
- BGAs with an intact package removed from the products that do not work to fix the device,
- Second-hand or refurbished BGAs bought from reliable suppliers,
- BGAs with broken solder balls damaged from improper operations or storage.
The key to decide whether the BGA deserves reballing is the functionality of the chip. How to tell if the BGA chip is good? Microscope inspection and functionality testing are required before sending the BGAs to PCBONLINE for BGA reballing and one-stop PCBA assembly.
First, removing the BGA from the original PCB carefully by heating the connection with a BGA rework station. Only if you don't have any access to a BGA rework station, can you use a hot air gun, which may damage the BGA due to manual operations.
Then, visually check the BGA package to ensure no cracks and use a microscope to further ensure that the appearance of the chip package is intact.
If you have any equipment to initially test the functionality of the BGAs, it would be better. But if not, it's also okay, as the one-stop PCBA manufacturer PCBONLINE can do the functional inspection before BGA reballing.
BGA Reballing Process
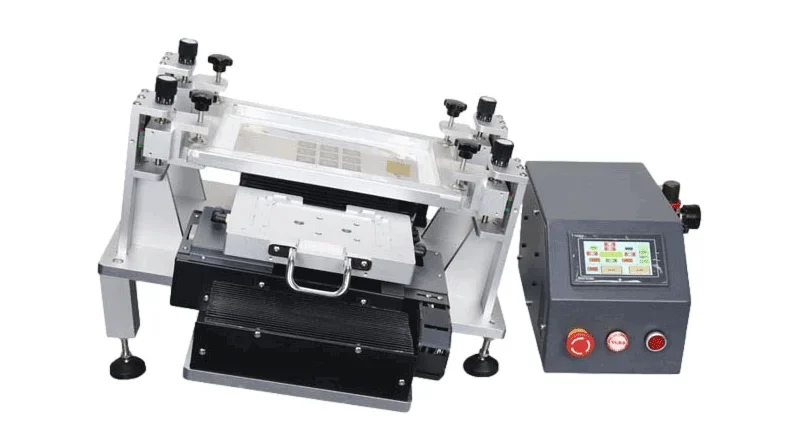
The principle of BGA reballing is attaching the solder balls onto the BGA pads. Below are the BGA reballing procedures.
Step 1. Place the solder balls
First, place the solder balls on the steel stencil and collect the extra balls with the ball placement tool shaking gently to let them fall into the collection tray. It ensures that each hole of the stencil accommodates a solder ball.
The balling needles are also prepared under the holes of the steel stencil.
Step 2. Spray flux to the BGA pads and prepare the BGA
Spray flux to the BGA pads. The flux will facilitate the solder balls sticking to the pads in the next steps.
Step 3. Position the BGA on the solder ball array
Use a vacuum sucker to lift BGA package by sucking its non-pad side.
Then the sucker positions the BGA on the steel stencil to align with the array of solder balls.
Step 4. Push the solder balls upward to attach the BGA pads
The balling needles under the steel stencil apply upward pressure and push the solder balls towards the BGA pads.
Due to the pressure applied by the balling needles and flux, the solder balls adhere to the BGA pads.
Now, the BGA is reballed with fresh solder balls.
Step 5. Check the solder balls of the BGA
Place the BGA on a flat surface and inspect the placement with an AOI (automatic optical inspection) machine. It ensures that all the solder balls are properly placed.
Step 6. Reflow soldering to consolidate the connection
Send the BGAs into the BGA heating machine for reflow soldering. The solder balls will consolidate onto the BGA pad tightly.
Finally, the extra flux at the bottom of the BGA is cleaned off with an ultrasonic oscillator.
The complete BGA reballing process is above. To avoid oxidation of the solder balls, the BGA should be surface-mounted as soon as possible. Otherwise, the BGAs should be stored with a bag of desiccant to prevent moisture.
BGA Reprogramming after BGA Reballing
A used BGA still has the existing firmware, and you need to reprogram to replace it with your new firmware.
BGA reprogramming can happen before surface mounting the BGA on the PCB. It can also be after PCB assembly.
The method for BGA reprogramming is IC programming, which works for both blank BGAs and used BGAs.
With IC programming, a second-hand BGA can replace its program or firmware.
For BGA reprogramming, you need to provide the below things:
- Your firmware or program. You can send it to us, and we won't use it for any other purposes. If you don't want us to access it, it's okay! When BGA reprogramming, you can upload your program via the cloud, and it is directly stored in the BGA without downloading it on our computer.
- A burner or programmer for the BGA and its adaptor cable. Of course, if you don't have such a jig, PCBONLINE can provide it.
After BGA reprogramming, the BGA works as brand new for your device.
At PCBONLINE, if it takes less than 30 seconds to reprogram each BGA, we offer BGA programming for free! If it takes longer, we charge only $0.1 for each BGA reprogramming.
BGA Reballing Service and PCB Assembly Under One Roof
If you need BGA reballing services for PCB assembly to create new products, you can work with the EMS (electronic manufacturing services) PCBA manufacturer PCBONLINE for BGA reballing and one-stop PCBA manufacturing.
Founded in 1999, the PCB EMS manufacturer PCBONLINE has two large advanced PCB manufacturing bases, one EMS PCB assembly factory, an R&D team, and stable supply chains. Besides, it has long-term cooperation with the top 3 mold manufacturers in China to manufacture the enclosures for box build assembly, SMT and BGA steel stencils, jigs, and molds for BGA reballing and PCB assembly.
PCBONLINE has complete testing and balling equipment for BGA reballing, from chip functionality inspections to reballing, PCB assembly, and BGA reprogramming.
For BGA PCB assembly, there's the X-ray inspection to ensure the solder balls are qualified for soldering and 3D AOI to ensure the PCB assembly quality.
One-stop EMS PCBA manufacturing custom meeting your project's demands, covering hardware and software R&D, prototyping/sampling, PCB fabrication, BGA reballing, component sourcing, PCB assembly, IC programming, and box-build assembly.
PCBONLINE offers free prototype/samples, R&D, and PCBA functional testing for mass production EMS PCBA projects.
High-quality EMS PCBA manufacturing certified with ISO 9001:2015, ISO 14001:2015, IATF 16949:2016, RoHS, REACH, UL, and IPC-A-610 Class 2/3.
PCBONLINE will ensure the success of your project, solve all issues and provide smooth BGA reballing and PCBA manufacturing.
No matter what application your project will be used for, such as automotive, industrial control, medical, military, aerospace, communication, computer, etc, you can work with PCBONLINE. To reach out to the OEM PCB manufacturer PCBONLINE, contact info@pcbonline.com.
Conclusion
This blog demonstrates the BGA reballing process. You can also learn about BGA reprogramming related to BGA reballing. To ensure the success of your PCBA projects and for BGA reballing, work with the EMS PCBA manufacturer PCBONLINE.
PCB assembly at PCBONLINE.pdf