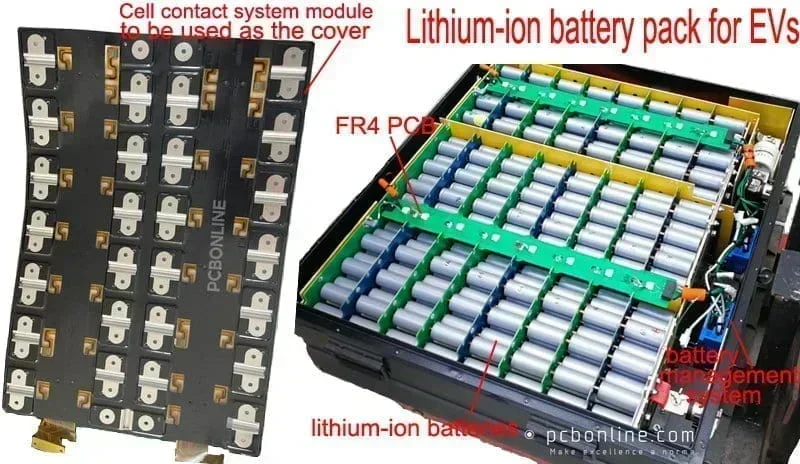
Lithium batteries provide power supply to electric vehicles (CV) and hybrid electric vehicles (HEV). How do you develop a lithium battery in your brand? PCBs are necessary for lithium-ion batteries for electric vehicles (EVs). In this article, you can read all about lithium battery PCBs, including what PCBs are used and where to use them in a lithium battery.
What does a Lithium Battery PCBA consist of?
To know about lithium batteries, you will understand the structure of a lithium battery module PCBA (printed circuit board assembly, a custom semi-product of all electronic products and systems) first.
A lithium battery PCBA is composed of many small lithium-ion batteries connected in series and rows, FR4 and flex PCBs mounted with required electronic components, and a battery management system (BMS). Inside the BMS, there is also a PCB.
What are the PCBs and the BMS used for?
Overcharge, over-discharge, too large currents for charging, short circuits, and too high temperatures during charging and discharging are not allowed for EVs and HEVs. Otherwise, the battery can break down. What's worse, the electric car may even burn.
PCBs and the BMS are used for monitoring the status of the lithium battery and protecting the battery from the above problems. Besides, the PCBs connect the batteries in series.
How do PCBs work in a lithium battery?
The PCBs between and on the four sides of the battery units and inside the BMS are FR4 PCBs.
On top of the lithium battery, there is a flexible PCB (FPC) cover that collects currents, temperatures, internal resistance, power amount left in the battery, and the working status (charging or discharging or not) of the battery. The FPC transfers these signals to the BMS.
Receiving signals from the FPC, the BMS takes measurements such as pausing charging to protect the battery.
You can imagine the FR4 PCBs and the FPC are neural networks, and the BMS is like the brain of the lithium battery.
The design for lithium battery PCBs is relatively simple. If you need a lithium battery PCB design, or if you are not sure whether your PCB design is okay or not, you can let our CAM engineer help you.
Why is FPC used for the cover of a lithium battery?
Flexible PCBs, or FPC, are used to transmit signals. They are lightweight and small in size and are easy to route and assemble in three-dimensional space. Besides, flexible PCBs increase the stability of a module.
In the above image, the white areas contact the unit batteries. An FPC is used because it is thin and easy to connect with the metal pieces, while an FR4 PCB can't do it.
FR4 PCBs used between lithium batteries and in the BMS
FR4 PCBs used between and on four sides of the lithium batteries and in the BMS have a high Tg. Tg is the glass transition temperature, and the higher the Tg, the higher the temperatures the PCBs can withstand. High-tg FR4 PCBs have a Tg of 180℃ and above.
Design Requirements for Lithium Battery PCBs
Reliability is the most important factor to consider in designing lithium battery PCBs. You will need to make the PCB reliability as high as possible.
Anti-vibration is another vital feature of lithium battery PCBs. Electric vehicles run on the roads, and not only the whole lithium battery module but also the whole car should be designed with anti-vibration for safety.
In regards to the quality standard of lithium battery PCBs, it is the ISO 16949 quality system. Lithium battery PCBs belong to automotive PCBs, and in the PCB industry, automotive PCB manufacturers must have the IATF 16949:2016 certification.
Lithium-Ion Battery PCB Fabrication and Assembly One-Stop Manufacturer - PCBONLINE
Frankly speaking, currently, Chinese factories have better manufacturing technologies for lithium batteries and electric car charging stations than factories in any other country in the world.
For lithium batteries, you can have the PCBs manufactured and assembled by the one-stop automotive PCB manufacturer PCBONLINE. PCBONLINE can also provide value-added manufacturing, including conformal coating and box build assembly, and delivers ready-to-use lithium batteries.
PCBONLINE has rich experience in electronic contract manufacturing for lithium batteries for electric vehicles.
PCBONLINE is an advanced PCB manufacturer and provides automotive PCBs such as high Tg FR4, FPC, rigid-flex, high-frequency, and metal-core PCBs.
If you want lithium battery PCB design, the CAM engineer from PCBONLINE can design the PCB for your project.
PCB manufacturing and assembly from PCBONLINE are certified with ISO 9001:2015, IATF 16949:2016, IPC, RoHS, REACH, and UL.
Besides one-stop lithium battery PCB manufacturing, PCBONLINE can help your product pass the qualification certifications.
PCBONLINE provides one-on-one engineering support and customer services throughout your project. The quoted prices are transparent and fair without any hidden costs. You can send your Gerber and requirements to PCBONLINE by email at info@pcbonline.com to get a quote.
Conclusion
PCBs are necessary for lithium battery manufacturing. FR4 PCBs connect the unit lithium batteries, and flexible PCBs collect and transmit lithium battery signals to the battery management system. Inside the BMS, there is also an FR4 PCB. The BMS monitors and manages the charging or discharging status of the lithium battery module. PCBONLINE is a professional and high-quality lithium battery PCB manufacturer, PCB assembler, and box build assembler. By working with PCBONLINE, you can yield lithium battery success.
©This article is an original work of the PCBONLINE team. Please indicate the author PCBONLINE if you reprint. If the article is reproduced without permission or indicating the author's source, PCBONLINE reserves the right to investigate the infringement.
Battery Management System Manufacturing at PCBONLINE.pdf
CCS Product Introduction - PCBONLINE.pdf