OSP is a commonly used surface finish on printed circuit boards (PCBs). However, OSP is not a generic surface finish on PCB pads for soldering, though it has many benefits for electronic soldering. As a PCB & PCBA manufacturer, we have received some PCB fabrication inquiries with inappropriate surface finish and we suggested changing the OSP to ENIG (immersion gold).
When to use OSP on PCB? What are the pros and cons of OSP? This article gives you answers below.
Part 1: What is OSP on PCB?
First, let's see what OSP is.
OSP, or organic solderability preservative, is a surface finish that is easy to oxidize. It is a thin and flat organic film applied to the PCB pads by a chemical method. During reflow soldering in the SMT assembly process, OSP is decomposed by the flux of solder paste and evaporates away. The bare copper pads are soldered with the melting solder.
The thickness of OSP is only 0.2microns to 0.5micons. The OSP materials can be rosin, active resin, and azole.
OSP PCBs should be assembled immediately after PCB fabrication, or they should be vacuum sealed in bags before putting them on the PCB assembly lines, in case the OSP surface finish goes bad and the copper pads oxidize.
Also, keep in mind that OSP PCBs can't be baked before PCB assembly. If the storage period of OSP PCBs is beyond 30 days, please ship the boards back to the PCB manufacturer to apply OSP again.
Part 2: Pros of OSP
OSP is a cost-effective PCB surface finish used widely. It has the below advantages.
- Appropriate for fine-pitch and BGA PCBs: compared with HASL, OSP has a small tolerance. Both OSP and ENIG are used for fine-pitch PCB assembly and BGA PCBs.
- Can be selective: OSP can be selective. For example, on the above HDI PCBs in the image, the light yellow pads use ENIG, and the dark yellow pads use OSP.
- Has good solderability: in reflow soldering, OSP is removed completely, and the bare PCB pads are directly soldered with the SMD components. The soldering effect of OSP PCBs is good.
- Cheap surface finish: applying OSP is at room temperature and easy. OSP is the cheapest PCB surface finish.
- Keep PCBA from thermal shock: when printed circuit boards at room temperatures go into the reflow soldering oven, the increased temperatures may cause thermal shock to the boards. OSP withstands thermal shock, and the copper pads avoid possible flaws.
Part 3: Cons of OSP
OSP is an organic coating easy to oxidize. You should know the below drawbacks of OSP.
- Easy to be scratched: OSP is thin and easy to scratch when carrying the boards. So the PCB manufacturer must take care when packing and operating the OSP PCBs.
- Easy to oxidize: OSP is easy to oxidize. If the OSP PCBs are not going to be assembled immediately, the PCB manufacturer seals each panel in a vacuum bag.
- Short storage span: the storage period of OSP PCBs is within 3 months.
- Many requirements for the storage environments: first, OSP PCBs should be sealed in vacuum bags. Second, in the bag, there should be a humidity instruction card and a desiccant. Third, the storage temperature is 15℃ to 35℃, and relative humidity is within 60%. Four, there's no acid gas in the storage environment.
Part 4: When to Use OSP as Your PCB's Surface Finish
OSP can be used both on simple printed circuit boards and complex PCBs, such as high-density IC load boards. You can use OSP as the PCB surface finish for the below cases.
1. Fine-pitch rigid PCB - If the rigid PCB pitch (center-to-center distance between adjacent pads) is within 0.5mm, HASL (including lead-free HASL) can't be used as the PCB surface finish, and you can use OSP or ENIG.
2. Flexible PCB - For FPC, OSP is used only less than ENIG, especially for flexible LED strips to reduce the fabrication cost. On FPC, you can use selective surface finishes - OSP and ENIG together for complex and high-performance applications.
3. Batch production for consumer electronics - OSP is cheap and has good solderability if the boards are soldered immediately. If you have a clear demand forecast and plan for bulky production, using OSP can reduce fabrication costs and achieve a good effect. Based on our experience, it is common to use OSP for batch fabrication of PCBs for consumer electronics.
4. Flexible aluminum PCB - Flexible aluminum PCB is a rarely used bendable aluminum substrate PCB used for LED lamps. Its power is 1W, and only OSP can be its surface finish.
5. Low-cost PCB fabrication - If you want to make the fabrication cost of your project to be as low as possible, choose OSP as the PCB surface finish. OSP PCB can also be used on high-frequency PCBs.
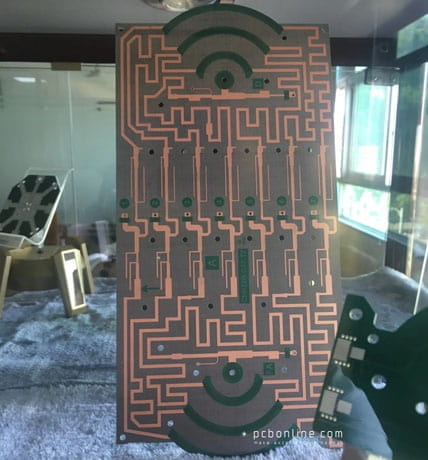
OSP high-frequency PCB made by PCBONLINE
You can't use OSP for keyboard PCBs, plug-ins (such as gold fingers), wire-bonding pads, PCBs that need multiple times for reflow, and PCB pads that need to expose the conductive area. Also, if your boards have to be stored for quite a long period, don't use OSP. What surface finish you can use for these situations? Keep in mind that selective ENIG can be used for all boards.
OSP Process
Reliable OSP PCB One-Stop Manufacturer - PCBONLINE
OSP has various materials and different performances. Choosing a reliable OSP PCB manufacturer is vital. PCBONLNIE, a one-stop PCB & PCBA source factory manufacturer, can be a reliable OSP PCB manufacturer for you. Founded in 1999, PCBONLINE has two large advanced PCB manufacturing bases and one PCB assembly factory.
PCBONLINE has many advantages in OSP PCB fabrication and assembly:
- We can manufacture BGA PCBs, HDI PCBs, high-frequency PCBs, FPC, rigid-flex PCBs, FR4 PCBs, and other boards with OSP and selective OSP PCBs.
- Our OSP PCBs are quality. The PCB fabrication and PCB assembly rigorously conduct the ISO/IAFT quality management system.
- PCBONLINE is certified with ISO 9001:2015, IATF 16949, IPC, REACH, RoHS, and UL. You can check out our business and quality certificates.
- We support PCB/PCBA fabrication and box-build assembly from samples to bulk production, and you can check the OSP PCB prototype effect before batch fabrication.
- We offer professional one-on-one engineering support through your project. When you quote from PCBONLINE, if your PCB uses OSP inappropriately, we'll give you improvement suggestions.
- Besides OSP, from PCBONLINE, ENIG, ENEPIG, lead-free HASL, carbon ink, immersion silver, immersion tin, silver plating, and selective surface finishes are available.
- Our experienced CAM engineer can help you reduce fabrication costs with an optimum PCB design.
For PCBs that should avoid oxidation and thermal shock, PCBONLINE provides nitrogen reflow and selective soldering on the PCB assembly lines. If you need cost-effective OSP PCBs/PCBA with good quality, please send your inquiry to info@pcbonline.com.
Conclusion
OSP is a cheap PCB surface finish with good solderability, but it is not generic. If you don't know whether OSP is suitable or not, ENIG always works for your PCB. This article reveals the pros and cons of the OSP finish on PCBs and when to use or not use it. If you need cost-effective PCB/PCBA fabrication with reliable quality, add PCBONLINE to your PCB supplier list.
© This article is an original work of the PCBONLINE team. Please indicate the author PCBONLINE if you reprint. If the article is reproduced without permission or indicating the author's source, PCBONLINE reserves the right to investigate the infringement.