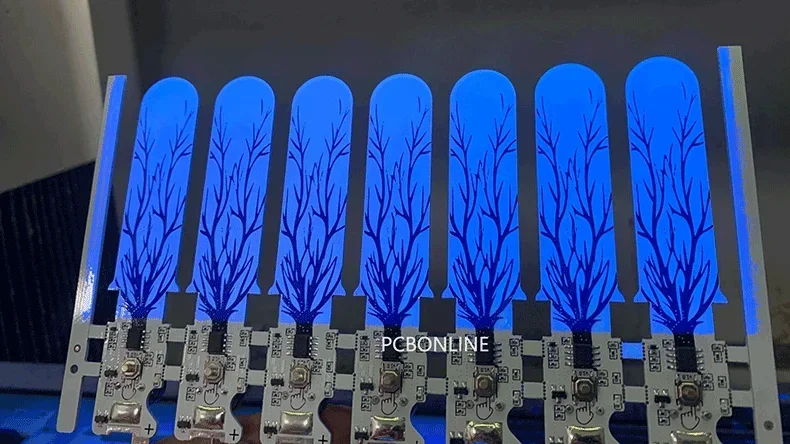
For applications requiring waterproofing, dustproofing, or vibration resistance, their printed circuit board or PCB is coated with a protective acrylic, polyurethane, parylene, or silicon layer. We call it PCB coating or conformal coating.
In this article, we will learn what PCB coating is, the applications of different PCB coatings, and how to apply conformal coating after PCB assembly.
In this article:
Part 1. What is PCB Coating Part 2. How to Apply PCB Coatings on the PCBA Part 3. One-stop PCBA Manufacturer PCBONLINE Provides PCB CoatingWhat is PCB Coating
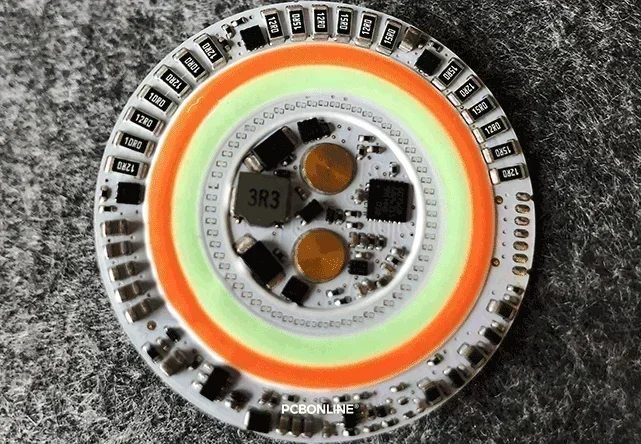
A PCB coating, also called conformal coating, is an acrylic/polyurethane/silicone/parylene coating applied on a PCB in the post-assembly stage.
Different PCB coatings have different characteristics.
Acrylic: Provides protection at a regular level and is used for not-so-harsh environments for consumer electronics. It is easy to remove for PCB repair.
Polyurethane: Has excellent resistance against chemicals, corrosion, and moisture but doesn't withstand high temperatures. It is suitable for PCBs working in outdoor and industrial environments. However, it is difficult to remove for PCB repairs.
Silicon: Has reliable resistance against high temperatures, moisture, and vibration. It's suitable for automotive electronics, aerospace/military equipment, and high-humidity environments like the sea and wild. However, its solvent resistance is at a regular level, so is not suitable for scenes requiring high chemical protection.
Parylene: This is a thin PCB coating providing comprehensive protection to the PCB from every aspect, including moisture, dust, chemicals, and vibration. It is used for high-end applications requiring precision and chemical resistance, such as high-corrosion environments, and medical, military, and aerospace electronics. Like silicon coatings, Parylene coatings are also difficult to remove for PCB repairs.
Epoxy resin: It is used less for PCB coating as it is easy to break in large temperature changes. However, the epoxy coating is rigid can can completely seal the PCB without any moisture going into it. It can be used in military electronics and marine electronics. It almost can't be removed for PCB repairs.
PCB coating belongs to the PCBA value-added services, including functional testing, IC programming, thermal aging testing, conformal coating, enclosures, and box-build assembly.
Why is a PCB sprayed with a conformal coating?
It is for protection against moisture, dust, chemicals, and vibration in harsh environments.
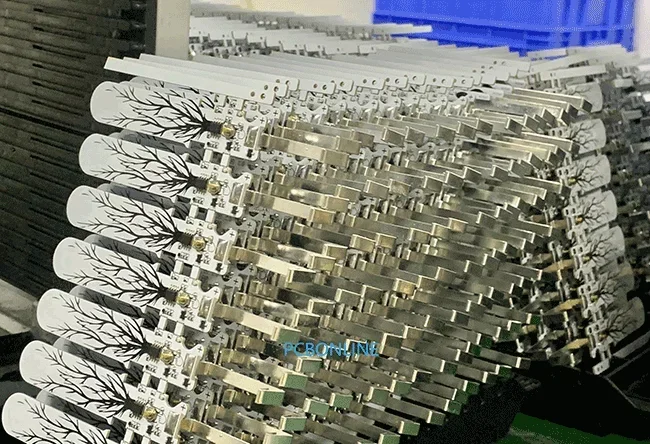
The benefits of PCB coatings for the PCBA and finished electronic products are:
Waterproof and moisture-proof
If a PCB needs to work in a humid environment like in the soil and near water, the area that may touch a small amount of water is applied with a conformal coating.
However, if the PCB works in a highly humid environment where water splashes on and even underwater with strong water jets, only applying a conformal coating on the PCB is not enough to meet the waterproof requirement.
Besides PCB coatings, the critical components on the PCB can be encapsulated with resin, the enclosure should be waterproof with a breathable membrane inside to prevent condensation inside the case, and the cable entry point should be secured with an o-shape silicon ring and thread locking.
Dustproof
Since PCB coating is waterproof, it is certainly dustproof. If your PCB is used outdoors or in dusty industrial environments, PCB coating can protect the circuit board from dust, conductive particles, static, and contamination.
Chemical resistance
If your PCB works in environments with chemicals, including acid, alkali, solvent, and gas corrosion, apply PCB coatings after PCB assembly. Especially, the Parylene PCB coatings provide the best chemical resistance, followed by silicon and epoxy.
Vibration resistance
A PCB coating can provide some protection against vibrations and impacts as it can, to a certain extent, absorb and cushion vibration shocks. Especially, silicon PCB coatings are soft and can be used for high-vibration environments like aerospace and military.
To sum up PCB coatings, below is a table of their resistances and applications.
PCB coatings
|
Water and dustproof
|
Chemical resistance
|
Vibration resistance
|
Removable for PCB repair
|
Applications
|
Acrylic
|
Average
|
Average
|
Average
|
✓
|
Indoor applications and consumer electronics
|
Polyurethane
|
Good but not resistant to high temperatures
|
Good
|
Good
|
Difficult to remove
|
Outdoor and industrial applications
|
Silicon
|
Very good
|
Average
|
Extraordinary
|
Difficult to remove
|
Automotive, aerospace, and high-humidity environments
|
Parylene
|
Extraordinary
|
Extraordinary
|
The ultra-thin layer cannot cushion vibration
|
Difficult to remove
|
Medical, high-end sensors, military, and high-reliability electronics
|
Epoxy resin
|
Very good but may break in temperature changes
|
Very good
|
Protective but not shock-absorbing
|
×
|
Equipment with high mechanical strength requirements
|
How to Apply PCB Coatings on the PCBA
In PCB assembly services, a PCB is assembled with all the required components to be a PCBA. If the PCBA needs protection from external adverse circumstances, the PCBA production panel is carried by a jig to be automatically sprayed with acrylic, polyurethane, silicone, or Parylene.
In bulky production, conformal coatings are automatically sprayed on the PCBA production panel, which panelizes multiple PCBAs.
The advantages of automated spraying are high precision, efficiency, and controlled thickness of the PCB coatings.
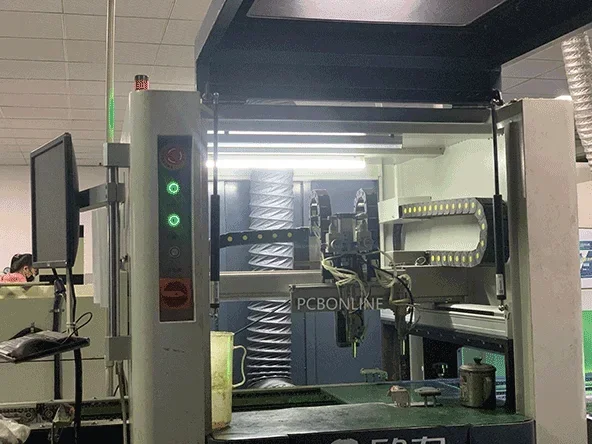
Then the liquid sprays are cured by baking to form the final PCB coatings.
If your PCB requires precision, there's PCB coating thickness measurement.
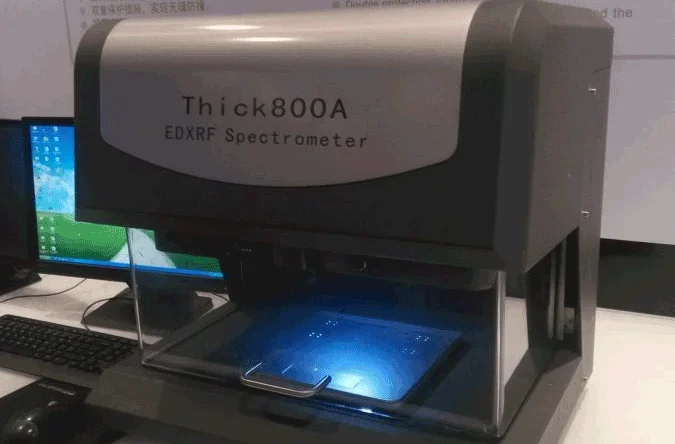
Besides, at the advanced PCBA manufacturer PCBONLINE, there's also the smart and selective conformal coating.
The selective conformal coating line not only automatically sprays and cures PCB coatings but also is equipped with a UV light inspection system to check the thickness of the coating.
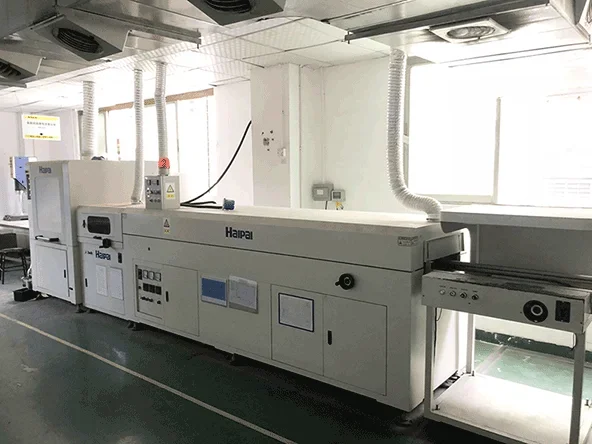
If you are working on small-batch PCBAs without thickness precision and many reliability requirements, you can also apply the liquid coatings by hand with a brush. However, the quality of PCB coating can't be consistent.
One-stop PCBA Manufacturer PCBONLINE Provides PCB Coating
If you're looking for a professional PCBA manufacturer that can apply PCB coatings and any other value-added services for your project, you can work with the turnkey PCBA manufacturer PCBONLINE from R&D to one-stop PCBA manufacturing and box-build assembly.
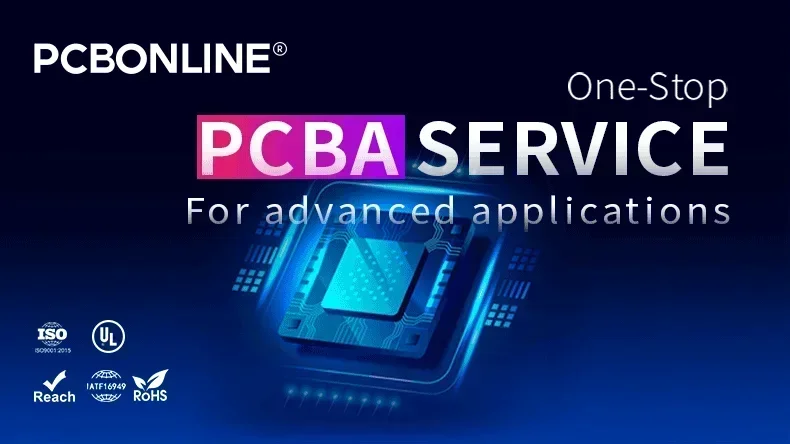
Founded in 1999, PCBONLINE has two large advanced PCB manufacturing bases, one turnkey PCB assembly factory for PCB assembly and box-build assembly, stable material supply chains and strategic cooperation with electronic component manufacturers, and long-term cooperation with the top 3 mold and enclosure manufacturers in China for jigs/fixtures, molds, and enclosures.
Besides, PCBONLINE has an R&D team and professional CAM engineers for project development and DFM (design for manufacturing).
PCBONLINE manufactures, assembles, and tests from PCBs to box-builds as a source factory manufacturer under one roof, from prototypes to bulky production, including conformal coatings.
Complete PCBA value-added services in the post-assembly stage, including PCB coatings, functional testing, thermal aging, IC programming, box-build assembly, and application simulation testing.
Provides one-on-one free and professional DFM (design for manufacturing) for PCB, PCBA, and box-build projects before and during prototyping/sampling to ensure the success of your project and seamless mass production.
PCBONLINE provides appropriate PCB coatings for your boards, including acrylic, polyurethane, silicone, Parylene, and epoxy.
PCBONLINE has a production line of PCB coating. Its automated machine can deliver your mass order quickly, and related UV light inspections are set for checking the conformal coating quality.
High-quality PCBA manufacturing certified with ISO 9001:2015, ISO 14001:2015, IATF 16949:2016, RoHS, REACH, UL, and IPC-A-610 Class 2/3.
When your project enters the bulky production stage, PCBONLINE refunds the fees of prototyping including its value-added services.
By working with the one-stop PCBA manufacturer PCBONLINE, you don't need to find other providers for value-added services, as all procedures, components, tests, jigs, and enclosures can be provided by PCBONLINE. No matter what application your PCB will be used for, such as automotive, industrial control, medical, military, aerospace, communication, agriculture, etc, you can work with PCBONLINE. To reach out to the turnkey PCBA manufacturer PCBONLINE, contact info@pcbonline.com.
Conclusion
PCB coatings are sprayed after PCB assembly and protect the assembly from moisture, dust, chemicals, temperature shocks, and vibrations. To ensure the success of your PCB/PCBA projects requiring conformal coatings, work with the turnkey advanced PCB manufacturer PCBONLINE.
PCB assembly at PCBONLINE.pdf