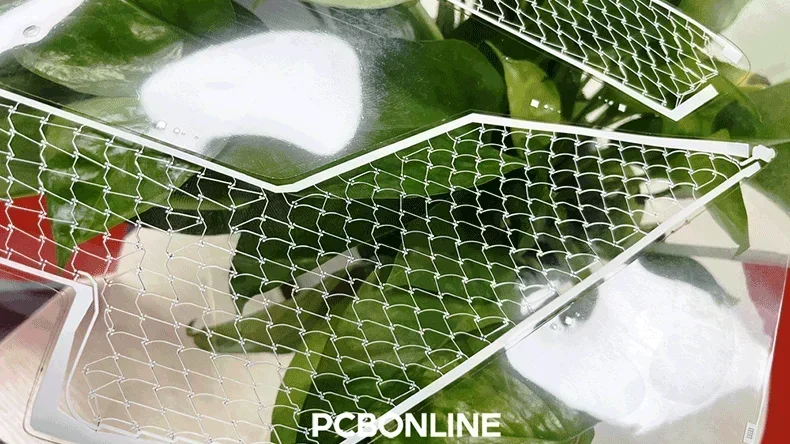
Unlike rigid circuit boards, flexible PCBs or FPCs bend, twist, and fold, but excessive bending can snap a trace or ruin the circuit. That is where the bend radius comes in. It is the minimum amount a flex PCB can bend before it gets damaged.
In laboratory biological equipment and many other electronic devices, transparency and flexibility are required for the PCB in the equipment. In scenarios requiring clearance, lightweight, small space, flexibility, and biosafety, use PET flexible PCB to build your system and devices!
In this article:
Part 1. What is PET Flexible PCB Part 2. Specifications of PET Flexible PCBs from PCBONLINE Part 3. Fabrication of PET flex PCBs Part 4. PET Flex PCB vs PI Flex PCBWhat is PET Flexible PCB
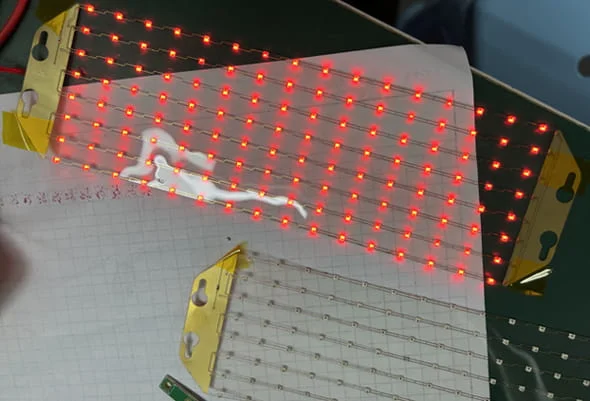
A PET flexible PCB is a transparent circuit board made of polyester material and flexible copper foil. PET is the base, insulation, and coverlay material for the board. The copper foil is laminated on the PET film and etched to be the circuit traces.
A PET flex PCB has 1 to 6 circuit layers. It features transparency, flexibility, lightweight, food safety, biosafety, and recyclability.
However, PET flexible PCBs can't withstand high temperatures.
All flexible circuit boards require reflow soldering to solder SMD components onto the boards. PET flexible PCBs have to be reflow soldered at low temperatures below 150°C.
Due to the low-temperature reflow soldering requirements, you should carefully select proper surface finishes and through-hole filling material for PET flexible PCBs.
Below are important properties/points of PET flexible PCBs regarding temperatures, through holes, surface finishes, and soldering:
1. PET flex PCBs can't be soldered by wave soldering but only by low-temperature reflow soldering below 150°C.
2. PET flex PCBs don't have traditional plated through holes (PTH) but non-plated through holes (NPTH). If a through hole of the PET flex PCB needs to be conductive, it is filled with silver, carbon ink, or conductive adhesive.
3. The solder paste for PET flex PCB assembly is low-temperature solder paste (SnBi alloy solder with a 138°C melting point) or conductive adhesive.
4. If necessary, the PET flex PCB can even not be soldered but connect the components through ZIF connectors by press connection.
5. The surface finish for PET flexible PCB SMT soldering is OSP or ENIG. Silver plating is not recommended to be the surface finish because silver ions diffuse easily.
6. If the pad of the PET flex PCB is not designed for soldering but a conductive button, its surface finish can be carbon ink.
7. The working temperatures of PET flexible PCBs are -25°C to +75°C. So if you plan to develop a high-power LED light, don't use PET flex PCBs but metal-core or even ceramic PCBs.
Specifications of PET Flexible PCBs from PCBONLINE
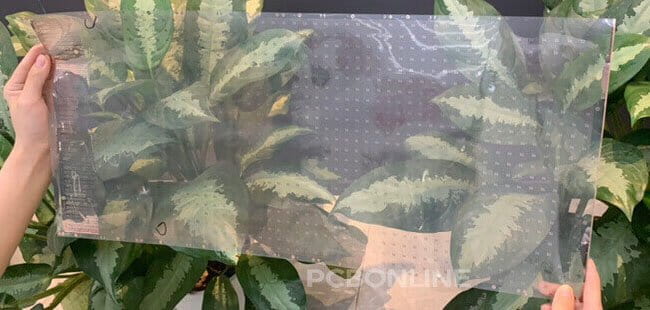
PCBONLINE is an advanced PCB/PCBA manufacturer, providing PET flexible PCBs, PI flexible PCBs, and rigid-flex PCBs and their turnkey assembly until the final product delivery.
PCBONLINE has manufactured and assembled many PET flexible PCBs for automotive lights, glass light walls, LED displays, wearables, biological lab equipment, animal trackers under the skin, etc.
Our PET flexible PCB specifications are below.
- transparency up to 85 %
- 1 to 6 layer transparent circuit boards
- finished clear flex PCB thickness: 0.1 to 0.6mm
- copper thickness: 18um, 35um, 70um
- surface finish: ENIG, OSP, ENEPIG, immersion tin, immersion silver
- surface finish: ENIG, OSP, ENEPIG, immersion tin, immersion silver
- min laser blind hole: 0.075 mm
- min mechanical drilling hole: 0.1 mm
- min line width: 0.035 mm
- min line spacing: 0.035 mm
- max blind hole aspect ratio: 0.8
- min interlayer alignment: ±0.05mm
- heat resistance for soldering: 150 °C × 5 sec.
- adhesive strength: 490 N/m
- operating temperature: -25°C to +75°C
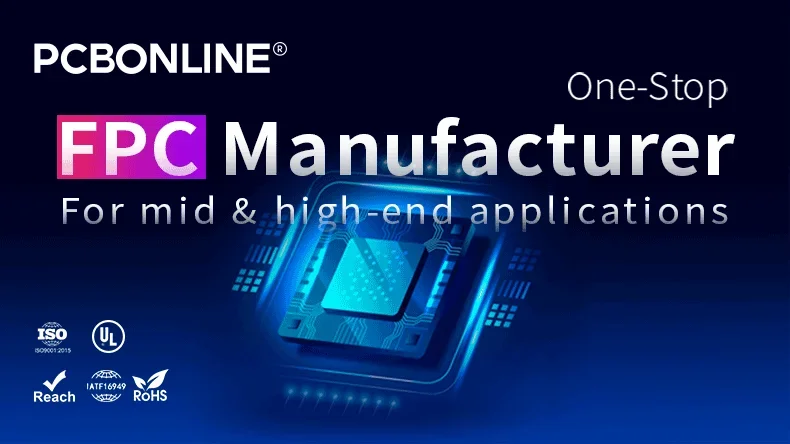
There are no quantity requirements for the PET flex PCBs at PCBONLINE, from prototypes to bulky production. To get a quote, please contact info@pcbonline.com.
Fabrication of PET flex PCBs
PCBONLINE provides one-stop PET flexible PCB manufacturing.
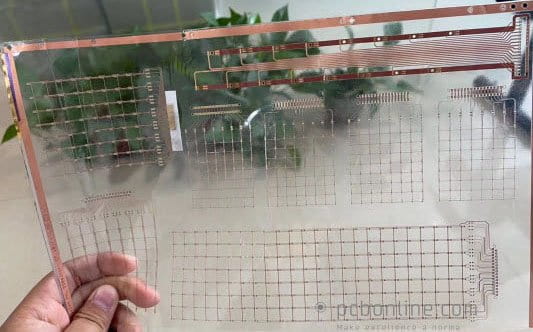
To illustrate the fabrication of PET flexible PCBs, take single-layer PET flexible PCBs with the OSP surface finish as an example.
First, the PET film is laminated to the required thickness and brushed with adhesive in the designated thickness. The coverlay consisting of a PET layer and an adhesive layer is also laminated in the required thickness.
The flexible copper foil in the required thickness is laminated on the PET film and silkscreen printed with a photoresist aligned with the circuit graphic from the development and exposure process.
Then the copper layer is etched to be the circuit copper traces and applied with the OSP surface finish.
After a circuit layer is completed, there's the AOI (automated optical inspection) to ensure the circuit is good.
If there are through holes that need to be conductive, the laminated board is laser drilled and then filled with silver or conductive adhesive.
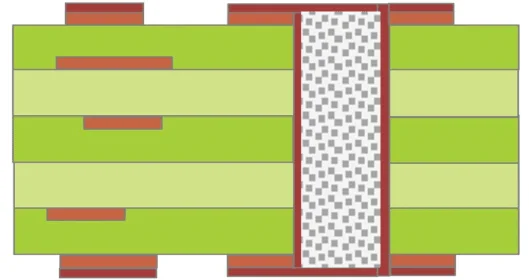
If the PCB pad is rectangular, its corresponding area in the coverlay is mechanically pressed with a model to form an oval-shaped hole to accommodate the pad without harming it. If the PCB pad is round or square, the corresponding hole in the coverlay is the same size.
Next, the coverlay is attached to the PET PCB layer and laminated to be the initial PET flex PCB.
If the are NPTHs, the PET flex PCB is mechanically pressed with a model.
Finally, there's the final check to ensure the PET flex PCBs are qualified for assembly and product applications.
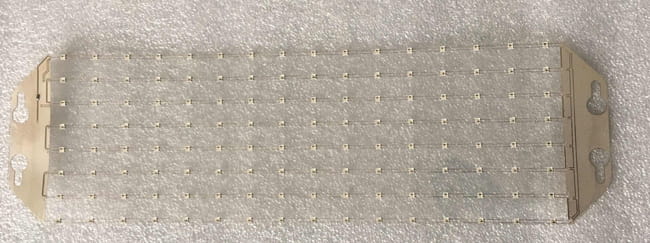
Regarding PET flex PCB assembly, there's only SMT assembly. As flexible PCBs easily move and warp during assembly, they are fixed on a board throughout the process. If the PET flexible PCBs are not assembled shortly after fabrication, they need to be baked before assembly. Besides, reflow soldering for PET flex PCBs is below 150°C, so the PCB manufacturer PCBONLINE uses the residual heat from the reflow of other circuit boards to solder PET flex PCBs.
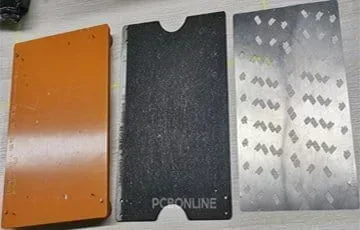
Except for the above three differences with rigid PCBs, the SMT assembly process for PET flex PCBs is the same as other circuit boards, including solder paste printing, solder paste inspection, LED and other SMD component pick-and-place, reflow soldering, and AOI to ensure the PET flexible PCBA is good.
In the post-assembly stage, PCBONLINE provides functional testing, thermal aging testing, burn-in programming, enclosures, and box-build assembly.
PET Flex PCB vs PI Flex PCB
Compared with PI flex PCBs, which are common, PET flex PCBs are used less because they don't provide many benefits except transparency. Check are a comparison between PET flex PCBs and PI flex PCBs.
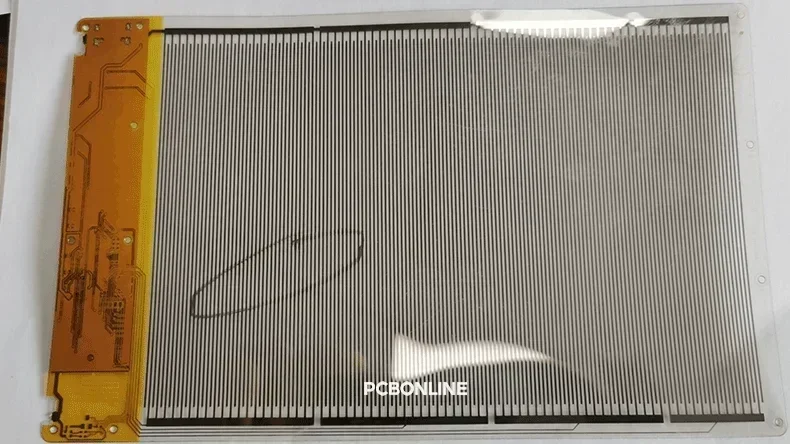
What they have in common are:
Both PI and PET flexible PCBs are made of bendable materials for compact space and lightweight.
Both support single and multilayer designs and can be single and double-sided.
Both require a jig board to fix them during assembly.
Both flexible PCBs feature certain chemical resistance and can be recycled.
The common surface finished for both are OSP and ENIG.
What they are different in are:
PET flexible PCBs are transparent, while PI flexible PCBs are yellow, black, or white (depending on the coverlay color).
PI flex PCBs have better heat resistance than PET flex PCBs.
So PI flex PCBs can be soldered by regular reflow soldering, while PET flex PCBs can only be low-temperature reflow soldered.
The working temperature range between PET flex PCBs and PI flexible PCBs is different. It is -25°C to +75°C for PET flex PCBs, while it is -20°C to +80°C for PI flex PCBs.
PI flexible PCBs made of RA copper can be dynamically and frequently bent, which PET flexible PCBs can't.
The chemical resistance of PI flexible PCBs is better than PET flexible PCBs.
Though the PCB cost depends on the circuit complexity and requirements, PET flex PCBs are generally more expensive than PI flex PCBs.
You can check the below table for a straightforward comparison between PET flex PCBs and PI flex PCBs.
PET flex PCB
|
PI flex PCB
|
|
Cost
|
Higher
|
High
|
Transparency
|
Yes
|
No
|
Chemical resistance
|
Good
|
Excellent
|
Flexibility
|
Good
|
Excellent
|
Circuit layers
|
1 to 6
|
1 to 8
|
Reflow soldering temperatures
|
Below 150°C
|
Below 210°C
|
Working temperatures
|
-25°C to +75°C
|
-20°C to +80°
|
Applications
|
Transparent LED lights, glass walls, transparent displays, biological observation equipment, automotive lights, wearables, etc.
|
LED lights, displays, automotive lights, smartphones, computers, wearables, medical equipment, beauty light masks, etc.
|
No matter what flexible PCBs you want, PCBONLINE can manufacture and assemble them according to your requirements and provide one-on-one engineering support and DFM. If you have questions about your flexible PCB project, feel free to ask us by email or from the online chat window.
Conclusion
PET flex PCBs are transparent flexible circuit boards made of polyethylene terephthalate. They are used for electronic devices requiring clearance. With PET flexible PCBs, you can create cool electric products that are transparent and flexible. However, PET flex PCBs can't withstand high temperatures. If you plan to design a PET flex PCB for a transparent application or are looking for one-stop electronics manufacturing for your completed design, work with the professional and experienced flexible PCB/PCBA manufacturer PCBONLINE with R&D and one-stop capabilities.