What is PCB solder paste? PCB Solder paste is a powdered mixture of flux and solder.
It is used to attach thousands of tiny electrical components to their contact pads in the assembly of printed circuit boards. Without it, the process of PCB assembly is incomplete.
If you're looking forward to designing and fabricating a PCB, read this article. It will take you through the crucial points you need to keep in mind while working with solder for PCB.
What Is PCB Solder Paste
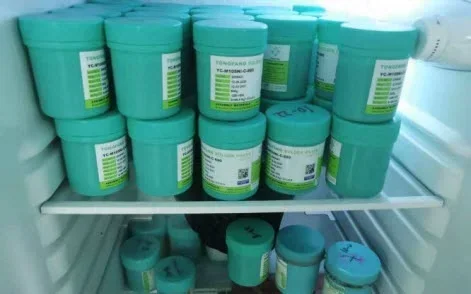
In electronics, solder for PCB is a substance used to join two or more components. Similarly, a solder paste has the same function, except that it is used in PCBs instead of the traditional copper boards, and it is in the form of a paste, which gives it some different properties.
Solder paste contains tiny particles of solder dispersed inside a past of solder flux. The paste is a mixture of different metals that is thick in consistency and can be easily applied to the printed circuit board while mounting its components. The flux holds the solder grains together for a smooth flow of current between the electronic components. It used to be a combination of lead and tin, but now manufacturers have started incorporating copper.
How To Choose Solder Paste For PCB Assembly
There are different types of solder pastes available in the market. Solder paste is classified according to the size of the particles it has. For example, a type 2 solder paste has more sizeable solder balls than a type 5 solder paste. As the type number increases, the size of the solder particle decreases.
Here are the solder ball sizes for each type:
Solder Paste Type
|
Size of Solder Particle (mm)
|
---|---|
Type 1
|
75-150
|
Type 2
|
45-75
|
Type 3
|
25-45
|
Type 4
|
20-38
|
Type 5
|
10-25
|
Type 6
|
5-15
|
Type 7
|
2-11
|
Type 8
|
2-8
|
All the solder particles present in the paste are not of the same size. We consider 80% of the total grains in a paste to fall in the classes mentioned above for our ease. You must be wondering how the particle size matters while choosing the right paste for your application.
The thing is, while working on smaller components, you would want the solder paste to have fine particles so that an even layer of tracks is formed.
If you use a type 3 solder paste to join small components, you might feel that the paths are uneven. Usually, types 3, 4, and 5 are used in electronics.
Another way to differentiate the solder paste is through their flux.
There are three types of fluxes used in solder pastes:
- Rosin - A rosin-based solder paste, as the name suggests, is made by using rosin. It is a substance obtained from pine trees. You can clean the excess flux using a solvent. It can not be cleaned with water.
- Water-soluble - This type of flux uses organic compounds. As the name suggests, it is water-soluble; hence you can clean it without using an additional solvent.
- No-clean - a no-clean solder paste, as the name suggests, does not need cleaning. You do not need to invest in other cleaning solvents. People most commonly use this type of flux because of the ease of use it offers and the low operating cost.
Choosing a solder paste depends entirely on your application. You can select the size of the solder particle according to the component size and then decide the type of flux you want to invest in. It depends on the user to choose the type of solder paste. There are no set guidelines for this purpose.
How To Store Solder Paste for PCB
Storing solder paste the right way is essential because it is sensitive to the temperature it's kept.
You will possibly end up damaging the solder paste if you store it at the wrong temperature. A deformed solder paste will not adhere to the printed circuit board surface, and unfortunately, you won't be able to mount your components on the board.
So, it's best to store it in an environment where the temperature is right.
According to a PCBA manufacturer PCBONLINE, the recommended temperature for storing the solder paste is between 2℃ to 8℃.
Not complying with the recommended temperature range will result in deformation.
Moreover, it would be best if you do not freeze it because doing so will damage the flux, and you won't be able to use it again.
Solder paste is stored at low temperatures to slow down the harmful oxidation process.
You might be wondering how to keep the solder paste.
Should you put it in a plastic bag or a container?
The answer is simple.
You need to make sure that the process of oxidation is slowed down, and for that to happen, you need to keep it away from oxygen.
So, the best way to store your solder paste is inside an air-tight container to keep oxygen away from it.
Like every other thing, solder paste also has an expiry date. It would be best if you don't use it after the date has passed because it will lose its properties by then and you won't get a good result.
How To Use Solder Paste for PCB?
Here comes the real question - how do we use solder paste?
The application of solder paste on the PCB is not an easy process. It requires great precision and accuracy.
The paste is only applied to some areas and not the entire board. So, while applying it, you need to make sure that the application is exact.
The process of applying solder paste can be made easier by using an SMT stencil.
So, the first step is to create the right stencil according to your circuit.
PCBONLINE manufactures the SMT stencils that match your PCB soldering best. All you need to do is provide us with your circuit Gerber file and leave everything to us.
The stencil makes sure that the solder paste is applied at specific locations in the right quantity. Using too much or too little paste will hinder the performance of your circuitry. Once you get your hands on the stencil, it is time to apply the solder paste.
At PCBONLINE, we let the solder paste stand for a few hours, typically 4-5 hours, to make sure the paste is at a temperature (22℃ to 28℃) where it can be used easily. If you apply cold solder paste on your PCB, it won't adhere to the surface, causing your components to fall off. But keep in mind that you can't heat the paste to raise its temperature. It must undergo a gradual temperature change to keep it from deforming.
This is how PCBONLINE uses solder paste in PCB assembly.
You need to apply the right amount of paste on the board. Too little will cause your components to fall off, while too much of it will cause the board to have uneven tracks, and the flow of current will get disturbed.
After applying the solder paste, the next stage is to place the components on the PCB. A pick and place machine is used for this purpose. It automatically picks components and places them in the right position on the PCB. You can do this manually, but you need to be careful not to place the component wrongly or in the wrong place.
Moreover, be careful not to mishandle the PCB at this point because that might lead to your components falling off the board, and you certainly do not want that to happen.
Note: It is recommended to let the board stay idle for a few hours till the paste has completely dried off and gripped the components as tightly as possible.
Further Reading: How Solder Paste Is Used In the PCBA Process?
PCBA stands for Printed Circuit Board Assembly, and this process involves all the steps that lead to manufacturing a fully functional PCB. It also includes the tests that confirm whether the PCB is fit to use or not.
PCB uses Surface Mount Technology (SMT) to stick the components on the circuit board. These components are small compared to the normal ones, which means you need to be very careful while placing them. For instance, if you compare an SMT IC with a normal one, you will notice that its body is smaller, and the legs are shorter. You need to be careful while soldering the short IC pins to ensure they are connected properly.
Step 1. The first step in PCBA is to apply solder paste on the bare board. It must be applied evenly to ensure that the current flows consistently throughout the board. At PCBONLINE, we use automatic solder paste printing machines for this task. Each bare PCB board in the machine has its stencil sitting on top.
Note: The distance between the solder paste printer and the board is important. Moreover, the angle at which the paste is dropped is also crucial. Keeping these points in mind will allow you to create the perfect PCB. At PCBONLINE, we have set standards to carry out these processes. We also recommend keeping the solder paste at room temperature for a couple of hours so that you achieve the right consistency to allow components to stick on the board surface
Step 2. After the solder paste is applied, you need to measure its thickness. The recommended range is between 0.09mm to 0.15mm. An SPI machine is used for this task. It closely measures how thick the solder paste is and alerts you if the range is exceeded.
For mounting the components, a high-speed mounter is used for small components such as resistors, capacitors, diodes, triodes, inductors, and small ICs. The mounter makes sure to put the components in place and firmly adhere to the solder paste.
Step 3. Next, the larger components are placed on the PCB. These include connectors, USB connects, FPGAs, and BGAs. A functional mounter is used to place these components on the printed circuit board. After this step, the PCB goes through an X-ray scan to see if there are any cracks present or not.
Step 4. The PCB now goes through the reflowing process. A reflow machine is used, which can be set to work on different temperature settings. Once the circuit board is placed inside the oven, the temperature is gradually raised to make sure the solder paste sets in perfectly, and then the board is cooled down, making sure that all the components and pads are fixed firmly.
At PCBONLINE, we take care of the circuit board by gradually raising the temperature and not letting the heat destroy the delicate circuit components. Our special reflow oven ensures your PCBs remain safe.
You can enjoy wonderful one-stop PCB manufacturing and assembly services at PCBONLINE. We can manufacture and assemble any circuit board. No minimum quantity requirements. If you feel interested in our services, get a quote online.
Conclusion
Solder paste is a very crucial part of the PCB assembly process. Without it, the entire process is incomplete because you won't be able to mount your components on the board. It is also essential to choose the right type of solder paste, that exactly matches your application. Using the wrong type of solder paste will get you into trouble because your circuit board will not function correctly.
It is best to get your solder paste applied by a professional. At PCBONLINE, we have well-trained engineers and technical staff who know what it takes to assemble the best PCB. You can trust us with all your PCB needs. All you have to do is tell us what your circuit looks like so that we may provide a quote instantly.
PCB assembly at PCBONLINE.pdf