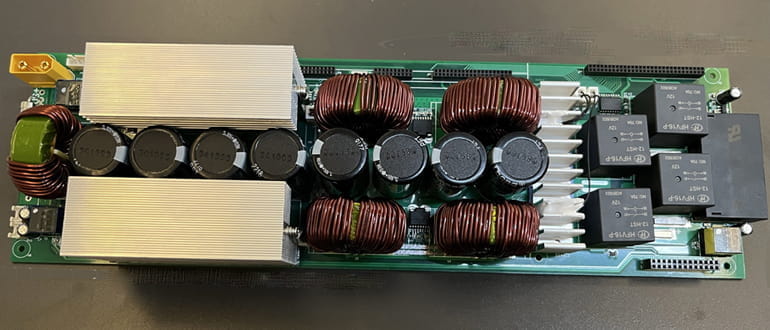
Through-hole PCB assembly is one of the PCB assembly technologies.
As electrical circuits are getting denser, the other PCB assembly technology -- SMT assembly is put to more use.
However due to the benefits of through-hole PCB assembly, typically, SMT and PTH PCB assembly technologies are both used in the PCB assembly process.
In this article, you will get an insight into through-hole PCB assembly, including what through-hole components and assembly are, the through-hole PCB assembly process, the pros and cons of through-hole PCB assembly, and applications of through-hole PCB assembly.
Part 1: What is Through Hole PCB Assembly
Through-hole PCB assembly, also known as PTH assembly, is a PCB assembly technology that connects the PTH components and the PCBA by inserting the component leads through the pre-drilled PTH holes.
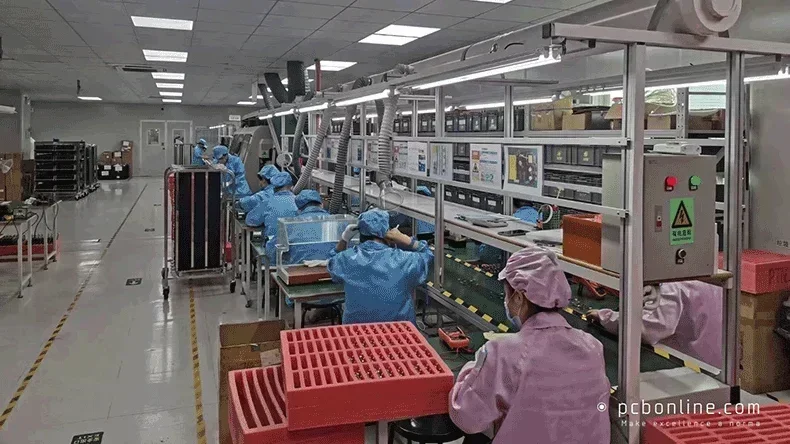
PTH holes are plated through holes that are mechanically drilled, and their hole walls are plated with copper during PCB fabrication.
PTH components, also called DIP (dual in-line package) components, have two and above long leads.
Most PTH components are radial components, which means their leads are in the same direction.
In through-hole PCB assembly, these PTH components are inserted into the PCB holes manually.
Some DIP components can be mounted on the PCB by the PIH (paste-in-hole) technology.
The ends of their leads are made pointy so that they can be pressed in the paste-in holes that are filled with solder and set up with standoff.
Part 2: How to Solve Challenges in PTH Assembly?
In your PTH assembly project, if you work with a PCBA manufacturer inexperienced in PTH assembly, your PCBA may have issues! Thus, choose an expert PTH PCB assembly manufacturer PCBONLINE that can solve all issues and ensure quality.
Issue 1. High Requirements for Industrial-grade PTH Assembly
For industrial-grade boards that require a large area of PTH assembly, such as the high-power industrial inverter board in the below figure, the PTH assembly requirements are high, including fullness and amount of soldering and overall thermal dissipation.
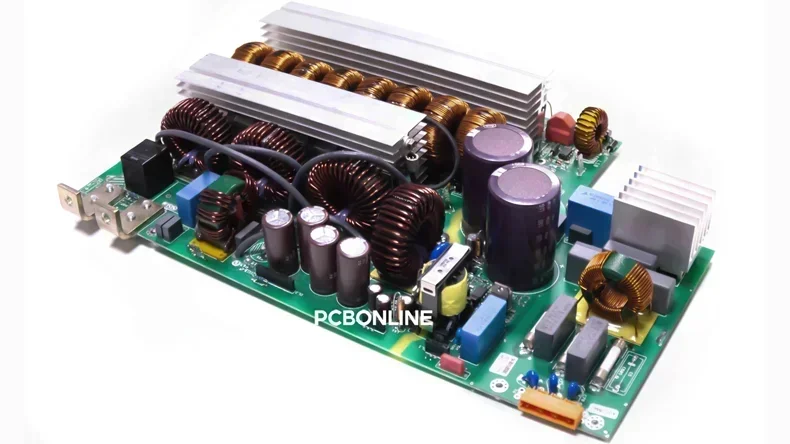
PCBONLINE can make high-power high-current PCBAs successfully because we skillfully design the jig/fixture for wave soldering and control the oven temperatures accurately to meet the PTH PCB soldering requirements.
Issue 2. Prevent the Floatation Issue in Wave Soldering
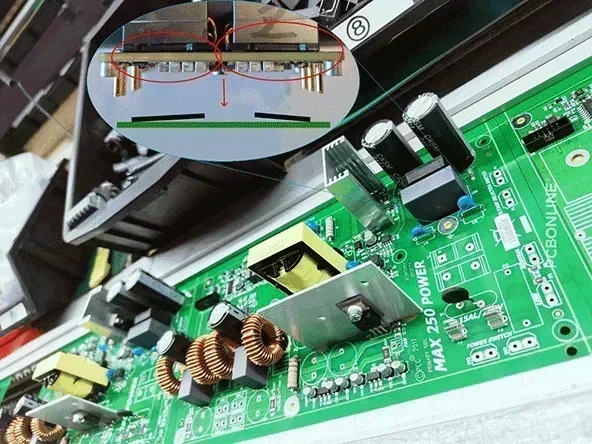
During wave soldering in the PTH assembly process, the PTH components may go up than the expected position like floating. This displacement phenomenon is called "floatation". It happens because of improper manual component placement and the thermal expansion of solder paste.
Floatation leads to gaps and uneven surfaces between components and the PCB, so the PCBA manufacturer must prevent it.
The professionals at PCBONLINE solve the floatation issue easily. Our solutions are:
- First, design the jig for wave soldering to press down the components that are easy to move during wave soldering.
- Second, apply a layer of adhesive to the component's bottom. Especially for PTH components that have to fit the product enclosure accurately, such as buttons and sockets, consider this method to prevent floatation.
- Third, if you have enough budget for your PTH assembly project, you can choose selective soldering to replace wave soldering. Selective soldering can prevent floatation and thermal shock and doesn't need a jig.
Part 3: Through Hole PCB Assembly Process
The through-hole PCB assembly process is half-automatic. It happens after the SMT assembly.
Typically, the through-hole PCB assembly process is:
Step 1. Inserting the leads through holes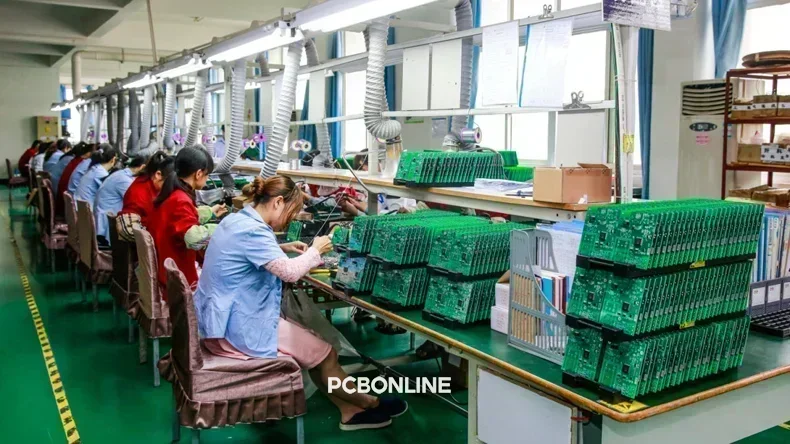
At this step, the technicians at the PCB assembly house press the PTH components to the end.
For most PCB assembly projects, there is a small quantity of PTH components on the PCBA.
For this reason, PCBA manufacturers choose the manual way to insert the PTH component leads through the PCB holes.
Step 2. Wave soldering or selective soldering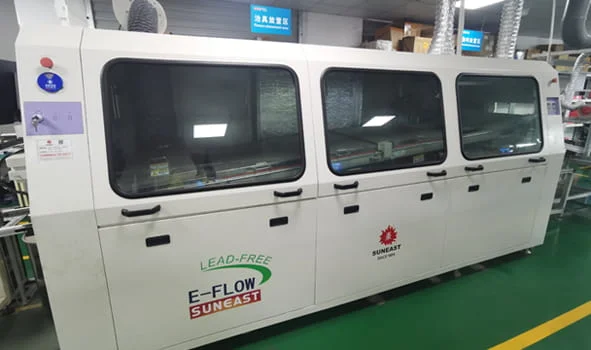
Before wave soldering, the PCBA is put in a jig, which insulates the PCBA except for the PTH holes from the external.
The PCBA is sent into the preheating oven before placing soldering.
At the preheating oven, the bottom of the PCBA is sprayed with flux and heated.
When preheating is done, the PCBA is sent automatically into a wave soldering oven or selective soldering oven.
In a wave soldering oven, the PCBA is dipped in the waves of liquid tin flows for 10-15 seconds.
If it is selective soldering, the ovens' muzzles solder the PTH components one by one.
Selective soldering prevents thermal shock and is suitable for PCBA whose components have different soldering requirements.
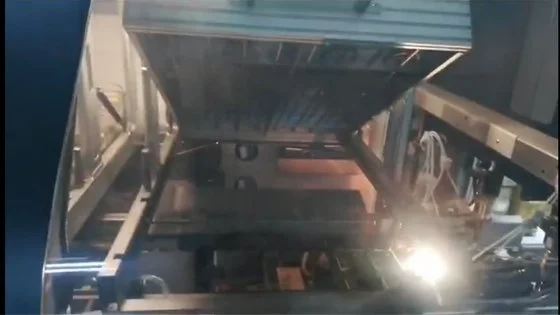
After soldering, the PCBA leaves the soldering line.
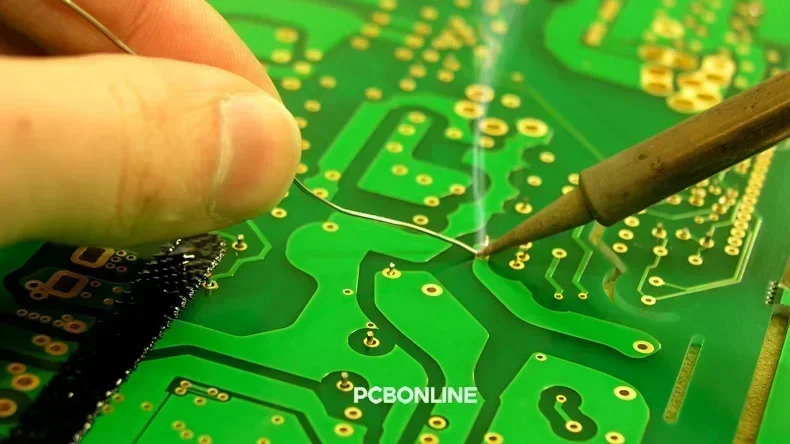
A technician trims the PTH component leads on the other side of the PCBA to be 1-2mm long.
Step 4. Clean and visual inspectionOn the PCBA, there may be flux residue.
Another technician next to the trimming technician cleans the PCBA surface if there's any residue.
Meanwhile, the technician visually inspects the PCBA.
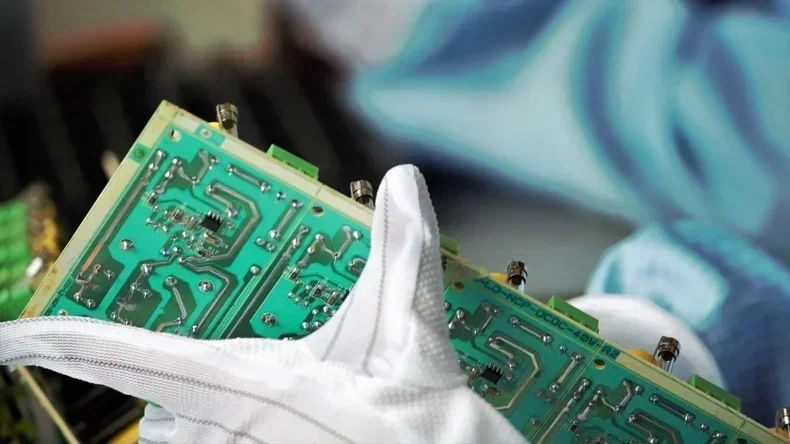
If any PTH components are not soldered fully, the technician uses a soldering iron to fix the soldering.
Step 5. Post-assembly tests and servicesAt the one-stop PCB assembly manufacturer PCBONLINE, post-PCB assembly tests and services are available, including:
- Conformal coating
- Functional testing
- IC programming
- Thermal aging
- Box build assembly
These PCBA tests and services ensure the functions, quality, and lifespan of the through-hole PCB assembly and the electronic products.
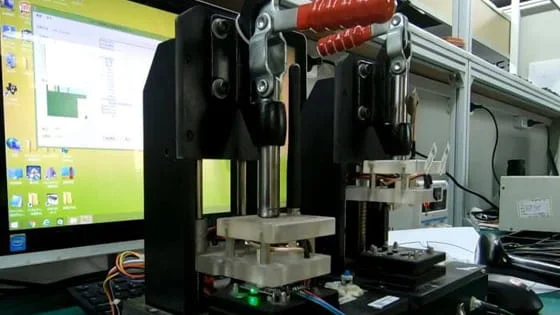
If the DIP components are soldered on the PCB in the PIH technology, the PCB assembly process is different:
Step 1. Printing solder paste in PTH holesThis happens on the SMT assembly line.
In a solder paste printing machine, solder paste is pressed by a scraper to go through the holes of the MST stencil to silkscreen print on the bare PCB.
The PIH holes are filled with solder paste. And on the PIH holes, some standoffs can support the DIP components.
Step 2. SPI (Solder paste inspection)The PCBA passes the SPI machine, which scans the solder paste on the PIH holes.
The machine compares the thickness, position, shape, and size of the solder paste with the reference. It ensures the solder paste in the PIH holes is qualified for soldering.
Step 3. Plugging in the holes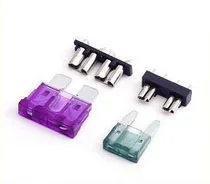
Press the DIP components to insert the solder-filled PCB holes.
Step 4. Reflow solderingThe PCBA is sent into the reflow oven to preheat and bake to melt the solder.
At the reflow peak, the solder, component leads, and the hole wall copper form a metallic compound, which marks the success of soldering.
Part 4: Pros and Cons of Through Hole PCB Assembly
Through-hole PCB assembly forms a strong connection between the PTH holes and the DIP components.
PTH assembly has below advantages:
- Solid connection between components and the PCB
- High durability against vibrations in high-speed operations
- Economic for PCB prototype and small-batch PCB manufacturing
- Suitable for mounting high-voltage, high-power, and high-mechanical-stress components, such as connectors, transformers, and electrolytic capacitors
However, compared with SMT assembly, through-hole PCB assembly has many drawbacks, including:
Space constraints: Through holes penetrate the PCB board. The space for trace routing is limited.
Not suitable for high-density and fine-pitch assembly: The trace width and space of the though-hole PCB assembly is large.
The size of DIP components is much larger than SMDs (surface-mount devices).
Through-hole PCB assembly is not suitable for dense circuits and small gadgets.
Not suitable for high-volume PCB assembly: Through-hole PCB assembly is manual.
If the PCBA project is high-volume production, PTH assembly is not suitable because of the lower efficiency.
Part 5: Applications of Through Hole PCB Assembly
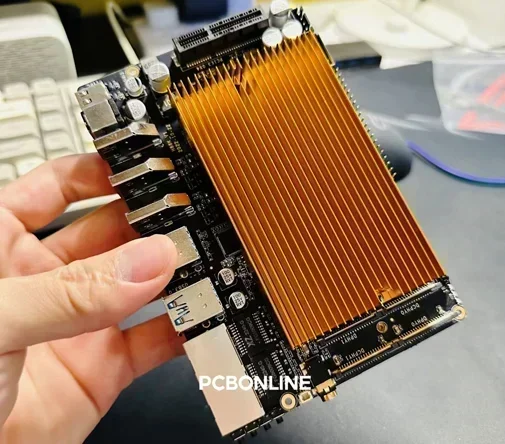
Through-hole PCB assembly is not suitable for high-density gadgets but suitable for high-power and high-voltage applications.
The space of the applications that through-hole PCB assembly is suitable for is large.
The applications that through-hole PCB assembly suit for include:
- Electricity supplies
- Industrial control boards
- High-power industrial inverter boards
- Chargers and charging stations for electronic cars
- Automotive communication control boards
- Audio and video decoding motherboards
- Thermal dissipation system for CPU/FPGA whose calculation value is large
Part 6: One-Stop Through-Hole PCB Assembly Manufacturer
Due to the large area of through-hole assembly, the requirements for solder fullness, tin intake, and overall heat dissipation system are high.
In such a case, you'll need a professional PCB assembly manufacturer to provide through-hole PCB assembly.
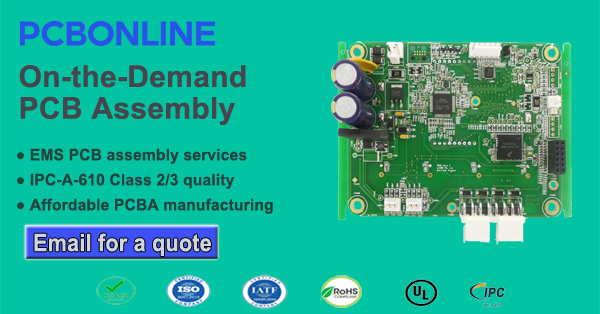
PCBONLINE is a one-stop PCB assembly manufacturer with expertise, rich experiences, and strong manufacturing capabilities for through-hole PCB assembly.
PCBONLINE pays attention to details of through-hole PCB assembly, such as jig design, soldering oven temperature control, and production procedure design. This leads to PTH assembly success.
At PCBONLINE, wave soldering and selective soldering are both available for through-hole PCB assembly.
One-stop PCBA and ODM manufacturing because PCBONLIE is a source factory manufacturer providing R&D, PCB fabrication, component sourcing, PCB assembly, and box-build assembly.
Low-cost and high-quality PCB assembly and electronics manufacturing at PCBONLINE.
Offer a free PCBA sample and functional testing for bulk production.
PCBONLINE has many successful PCB assembly, ODM, and OEM manufacturing experiences, including high-power industrial converter boards, industrial HD cameras, electronic car chargers, EV charging piles, industrial controllers, and so on.
If you have any PCB assembly manufacturing needs, contact PCBONLINE at info@pcbonline.com.
Conclusion
Nowadays, as electronic gadgets have a smaller size and higher circuit density, through-hole PCB assembly is gradually replaced by SMT assembly. However, due to the rugged connection, through-hole PCB assembly is still used for many high-power equipment and military applications that work in vibrations. If your PCBA project needs SMT and through-hole PCB assembly, work with a reliable PCB assembly manufacturer PCBONLINE that can save your costs and provide the best quality products.