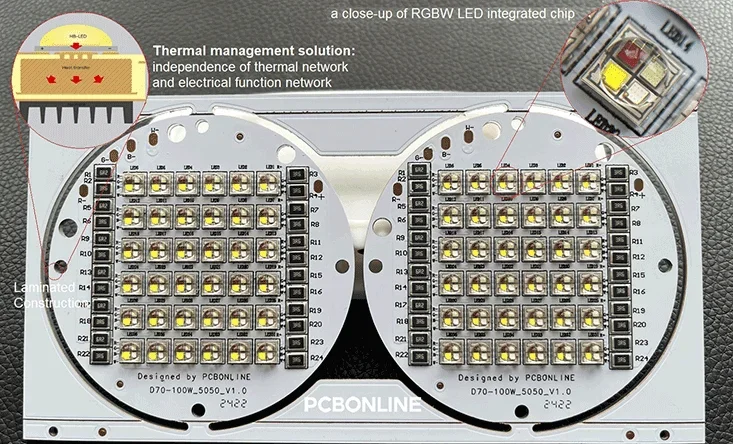
waterproof RGBW LED light designed and manufactured by PCBONLINE for underwater lights
Have you ever wondered how underwater or outdoor electronic systems operate? Moisture is the biggest enemy of electronic circuit boards, how are Printed Circuit Boards (PCBs) designed to be waterproof? This article will explore waterproofing PCBs, highlighting various PCB waterproof methods and their applications.
In this article:
Part 1. What are Waterproof PCBs? Part 2. Methods of PCB Waterproofing Part 3. Applications of Waterproof PCBs Turnkey Waterproof PCB Manufacturer PCBONLINE with R&D CapabilitiesWhat are Waterproof PCBs?
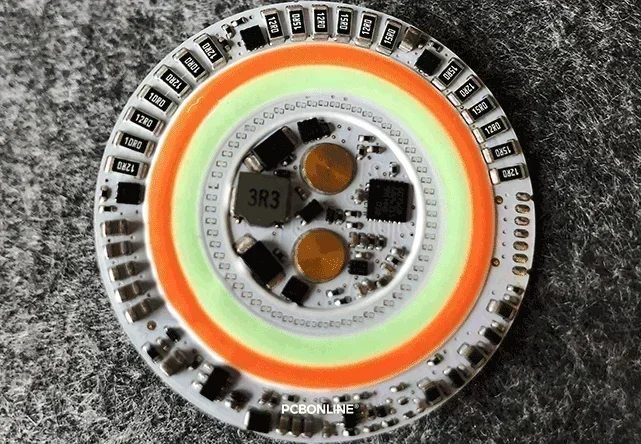
ceramic waterproof PCB manufactured by PCBONLINE for swimming pool lights
Waterproof PCBs are usually high-Tg FR4, PTFE, metal-core, or ceramic PCBs protected against moisture. Waterproof PCBs have no sharp corners or a large area of exposed copper. Their surface finishes are usually ENIG or OSP.
The circuit board waterproofing methods include selective resin encapsulation + wire entry point waterproof design, conformal coating, IPX8 waterproof enclosure, or even entire resin encapsulation to seal the PCB and the internal of the device.
Waterproofing PCBs help safeguard electronic devices from moisture damage, water exposure, and extreme weather conditions, extending their lifespan in tough environments like marine, military, and industrial settings. The waterproofing coating/spray, resin encapsulation, and additional waterproofing protection ensure reliable performance, preventing corrosion and electrical failures.
Different environments and waterproofing requirements require different waterproofing methods. Below are the PCB waterproofing methods for different waterproofing requirements/environments. The application examples are also below.
1. Applications working in not very humid environments, including in soil, near water or the seashore, and outdoors. Examples are moisture sensor boards under soil for automatic plant watering.
The method for waterproofing electronic circuit boards in not very humid environments is a conformal coating or spraying for regular resistance against moisture.
2. Applications working in shallow underwater, the application example is swimming pool light, or on the river or sea where water splashes onto the device intermittently, the application example is yacht lights.
The method for waterproofing the circuit boards in shallow underwater or on the river or sea is PCB selective PCB encapsulation with resin + additional waterproof measures (O-ring silicon sealing gasket + waterproof thread locking at the cable entry point).
3. Applications working deep underwater, the application example is deep sea lights.
The method for waterproofing the PCB is potting or casing encapsulation + additional thermal management.
Note: Encapsulation means immersing a PCB in a protective material, resin. It can be fully submerging the board or selectively applying protective layers to specific areas resin encapsulation offers greater protection than selectively applying conformal coatings.
Designing waterproof PCBs should not only consider waterproofing the circuit boards and enclosures but also thermal management and long-term operation. To learn about waterproof PCBs, check details for the methods of waterproofing circuit boards in the next parts.
Methods of PCB Waterproofing
The above content mentioned the PCB proofing methods for different working environments. Let's deep dive into these PCB waterproofing approaches for comprehensive understanding.
Conformal coating
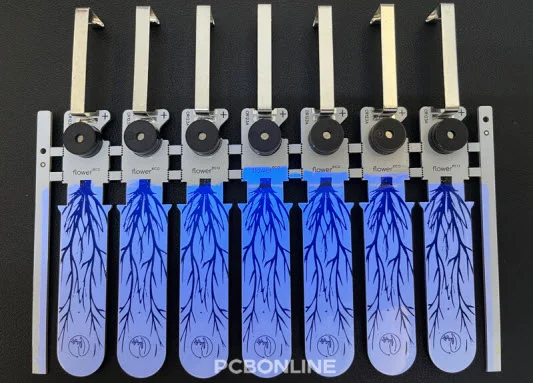
automated watering PCBA inserted in soil manufacturer by PCBONLINE
Waterproof applications: for not very humid environments
The waterproof conformal coatings for PCBs include acrylic, silicone, polyurethane, epoxy, and Parylene. They are synthetic resins that provide a secure barrier around a printed circuit board and its components.
Conformal coatings provide protection from moisture, fungus, dust, and other possible contaminants. They enhance dielectric strength, reduce mechanical stress on components, and protect a product from thermal shock.
Conformal coating is an auxiliary waterproofing measure. If the circuit board is used in a not very humid environment, like in the soil, conformal coatings work. However, if it is underwater, conformal coating is far from meeting waterproof requirements.
Achieving maximum benefits from conformal coatings requires coordination of the PCB design, coating selection, and application with the proper cleaning protocol. Here are the reasons to use conformal coating in your waterproof PCB projects:
- The circuit has to be used in a not-very-humid environment as it provides auxiliary protection from moisture.
- A thin and lightweight protective layer is needed for applications where weight is important, such as consumer electronics, drones, and portable medical devices.
- Frequent modification or repairs are needed because conformal coatings can be selectively applied and easily removed.
Selective PCB encapsulation
Waterproof applications: for shallow underwater and high-humidity environments like on the rivers or sea; should be used with other waterproof measures
Selective PCB encapsulation means using resin to seal specific components and areas rather than the whole PCB. It is waterproof and anti-vibration and allows the PCB to be repaired. It includes dam encapsulation and glop top encapsulation.
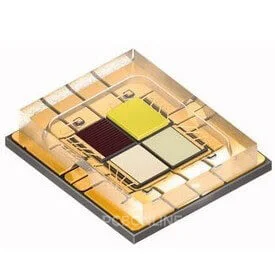
a) Dam and fill encapsulation
Dam and fill encapsulation is a targeted approach for PCB waterproofing. It protects selected components.
In this method, a quick-drying material is used to create a small containment barrier (a "dam") around specific components. Once cured, the encapsulating liquid is poured into this confined area, ensuring localized protection where needed and keeping the weight to a minimum.
In underwater applications like swimming pools, only the components like LEDs and power supply are encapsulation, and therefore Dam and Fill technique is used.
b) Glop top encapsulation
Global top encapsulation is a lightweight waterproofing solution for small components.
This method involves placing a small, highly viscous droplet of encapsulation material over a component.
The material forms a protective dome, making it ideal for selective applications.
However, it requires high-viscosity materials to prevent the unintended spreading of the encapsulation material. The glop top technique is generally used for targeted protection like semiconductor packaging.
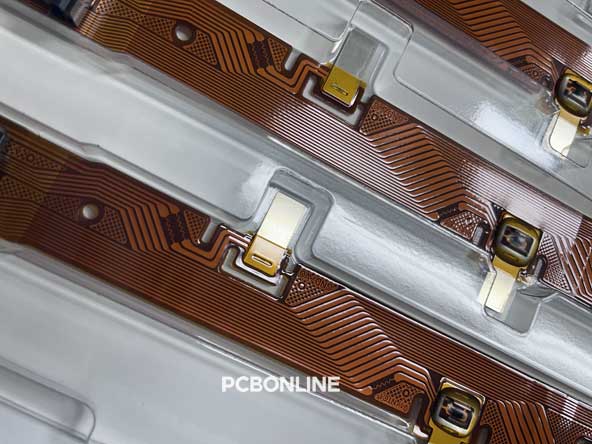
thermistor glop top encapsulation in the flex PCBA of the CCS
For the cell contact system (CCS) in the EV battery pack, glop top encapsulation is also used for waterproofing the thermistors in the CCS, which detects the temperature changes in the battery cells.
However, selective PCB encapsulation only waterproofs the components and areas it pours onto. For underwater applications like swimming pool lights and applications that water splashes on, selective PCB encapsulation doesn't make all the devices waterproof.
Besides selective PCB encapsulation, additional waterproofing measures are required for the waterproof PCB and device:
First, an IPX8 waterproof enclosure. It will be introduced in the next part.
Second, a silicon O-shape sealing ring at the cable entry point with a waterproof cable gland or thread locking. They prevent water from going through the cable entry point into the device.
Third, a waterproof breathable membrane in the enclosure to avoid condensation inside the device.
Potting or casing PCB encapsulation
Waterproof applications: for extreme moisture exposure like deep underwater; the PCB should take care of thermal management
This method involves placing a temporary or permanent barrier around the PCB, and then pouring encapsulating liquid over the entire assembly. Once cured, the barrier may be removed, leaving the circuit board completely enclosed in a protective polymer.
This process deals with sealing the entire PCB in a thick resin layer. The materials commonly used for plotting compounds include silicone, polyurethane, and PCB encapsulation epoxy.
In the deep sea applications where the circuit board has to encounter a lot of water, the potting method is utilized.
However, potting encapsulation is not recommended for most cases as it affects thermal dissipation greatly and can't be fixed later on. In contrast, waterproof PCBs with selective encapsulation can be repaired.
If casing PCB encapsulation is a must, like in deep water environments, the PCB design must consider thermal dissipation with water cooling (heat conducted from the PCB to the high-thermal conductive resin to the Ti-Al alloy enclosure).
Besides, if the deep water application is an LED light, the high-thermal conductive silicon should be optical with a light transmittance ≥ 90%, and the enclosure area above the light source can be polycarbonate, acrylic, or transparent silicon for lighting.
The IPX8-standard enclosure for waterproofing
The enclosures to be assembled on waterproof PCBAs meet the IPX8 standard.
The IPX8 standard is an Ingress Protection (IP) certification of dust and moisture protection. It indicates how well a device can withstand exposure to dust particles and water. The "X" in IPX8 indicates the non-tested condition for dust while the "8" indicates the highest level of water protection.
An IPX8 enclosure means that the finished device can be submerged in more than 1 meter of water.
The following tables indicate the meaning of the first and second letters in IP ratings. The first letter indicates the protection against solid particles, while the second letter indicates the protection against water.
Solids:
X
|
Not tested
|
0
|
Not protected
|
1
|
Objects larger than 50 mm
|
2
|
Objects larger than 12.5 mm
|
3
|
Objects larger than 2.5 mm
|
4
|
Objects larger than 1 mm
|
5
|
Dust protected
|
6
|
Dust tight
|
Water:
X
|
Not tested
|
0
|
Not protected
|
1
|
Dripping water
|
2
|
Dripping water tilted at 15°
|
3
|
Spraying water
|
4
|
Splashing of water
|
5
|
Water jets
|
6
|
Powerful water jets
|
It is necessary to use an IPX8 enclosure for waterproofing PCBs as it provides industry-level water protection for components
From the above, we can conclude that a reliable and fixable way to waterproof PCBs is the dam and fill encapsulation + IPX8 enclosure + a combination of silicon sealing for cable inlets and waterproof thread locking. This combination stops water from entering the device through the cable inlet and enables you to repair the PCBs in the future.
For more reliability, the conformal coating can also be sprayed on the PCB.
Only in extreme water exposure environments like deep sea, potting encapsulation is used, which is unrepairable.
Applications of Waterproof PCBs
The devices working underwater or in high-humidity environments require waterproof PCBs, including:
- swimming pool lights,
- deep sea searchlights,
- remote-controlled underwater robots,
- ocean fish finders,
- water quality monitoring sensors,
- port navigation lights
- sewage treatment equipment, etc.
Devices working in not very humid environments also require waterproof PCBs, like:
- outdoor LED displays,
- transportation cameras,
- automated watering devices inserted in the soil,
- outdoor mining equipment,
- outdoor communication stations,
- solar energy charging controllers, etc.
A real-world application of waterproof PCBs - CoB LED
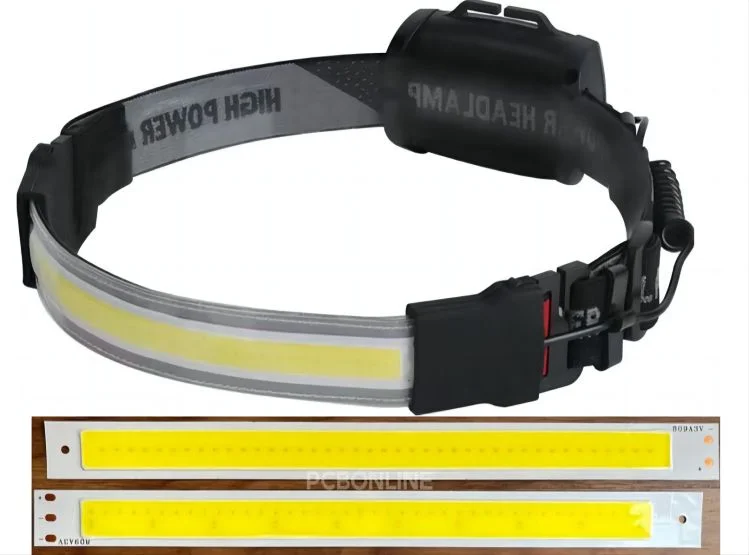
waterproof COB LED miners' headlight manufactured by PCBONLINE
A CoB LED (or chip-on-board LED) is a single device with many LED chips mounted on a thermally efficient substrate placed below a uniform phosphor coating. As a general rule of thumb, CoB LED lights are higher-quality light sources because they use reflectors to provide focused and controlled light.
For CoB LEDs, there are three waterproof ratings, including CoB LED IP65, IP67, and IP68. You can understand the IP ratings via the following info:
- IP65 CoB LED strip is resistant to dripping and splashing water, but the PCB can't contact with water.
- IP67 CoB LED strip is entirely waterproof and suitable for outdoor use, such as lighting your gardens. They can also be applied in bathrooms or kitchens where there is frequent water contact.
- IP68 CoB LED strip is suitable for use in underwater environments, perfect for lighting the border of swimming pools and fountains.
Silicone CoB LED strip, also called CoB LED neon strip, is a special kind of CoB LED waterproof tape light. It combines the advantages of both CoB LEDs and neon rope lights. These strips are highly flexible and resistant to breakage and offer exceptional water resistance simultaneously.
Turnkey Waterproof PCB Manufacturer PCBONLINE with R&D Capabilities
If your PCB or PCBA project needs waterproofing, no matter how humid the environment that the device is working in, you can work with the turnkey waterproof PCB manufacturer PCBONLINE from R&D to one-stop PCBA manufacturing and box-build assembly.
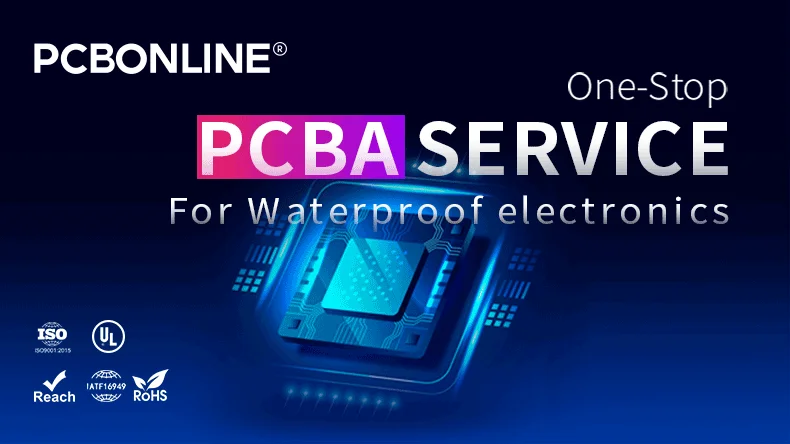
Founded in 1999, PCBONLINE has two large advanced PCB manufacturing bases for waterproof PCBs, one turnkey PCB assembly factory for waterproof PCB assembly and box-build assembly, stable material supply chains and strategic cooperation with electronic component manufacturers, and long-term cooperation with the top 3 mold and enclosure manufacturers in China for jigs/textures, molds, and waterproof enclosures. Besides, PCBONLINE has an R&D team and professional CAM engineers for project development and DFM (design for manufacturing).
PCBONLINE manufactures and assembles waterproof PCBs in various materials, such as ceramic, aluminum, high-Tg FR4, and PTFE.
PCBONLINE provides one-stop electronics manufacturing for waterproof PCBs and devices, from water PCB fabrication to enclosure installation on the PCBA, from prototypes to bulk production.
Whether it is underwater with powerful water jets or in not-so-humid environments like in soil or outdoors, PCBONLINE can manufacture waterproof PCBs that meet your project requirements.
PCBONLINE provides free and professional DFM (design for manufacturing) for waterproof PCB, PCBA, and box-build projects before and during prototyping/sampling to ensure the success of your project and seamless mass production.
High-quality waterproof PCBA manufacturing certified with ISO 9001:2015, ISO 14001:2015, IATF 16949:2016, RoHS, REACH, UL, and IPC-A-610 Class 2/3.
PCBONLINE will ensure the success of your project that requires waterproofing, solve all issues, and provide functional testing and application simulation testing.
PCBONLINE has brought out many waterproof PCBA and box build projects successfully, including automated watering PCBAs in soil, swimming pool lights, outdoor transportation cameras, highway indicator lights, airport outdoor LED displays, CCS for EV battery packs, etc. No matter what application your waterproof PCB project will be used for, such as automotive, industrial control, medical, military, aerospace, communication, agriculture, etc, you can work with PCBONLINE. To reach out to the turnkey waterproof PCB manufacturer PCBONLINE, contact info@pcbonline.com.
Conclusion
This blog introduces what a waterproof PCB is and circuit board waterproofing methods. Waterproofing is required for many electronic devices working in humid environments such as outdoors and even deep sea. To ensure the success of your waterproof PCB/PCBA projects, work with the turnkey advanced waterproof PCB manufacturer PCBONLINE.
PCB fabrication at PCBONLINE.pdf